Submitted by Glynn Bartlett on Mon, 04/26/2021
Typically, robots are not in service long enough to require “major” upgrades. In a typical robot’s service life, there may be some software updates and improvements to the end-of-arm tooling (EOAT) but no major changes. In contrast, some of the robots we have developed, operate effectively for decades. There are key lessons to be learned when planning for an extended robot life cycle with upgrades and retrofits that must be planned to keep the systems healthy and happy.
One example of a long-life system is the “Robotic Depaint System” (RDS) for aerospace coating removal. This system was installed in 1991 and is still stripping paint off aircraft today. The RDS, featured in the image below, is comprised of three nine-axis, large-workspace robots that have benefited from retrofits to electronics, software, motors, gearboxes, and motion control systems.
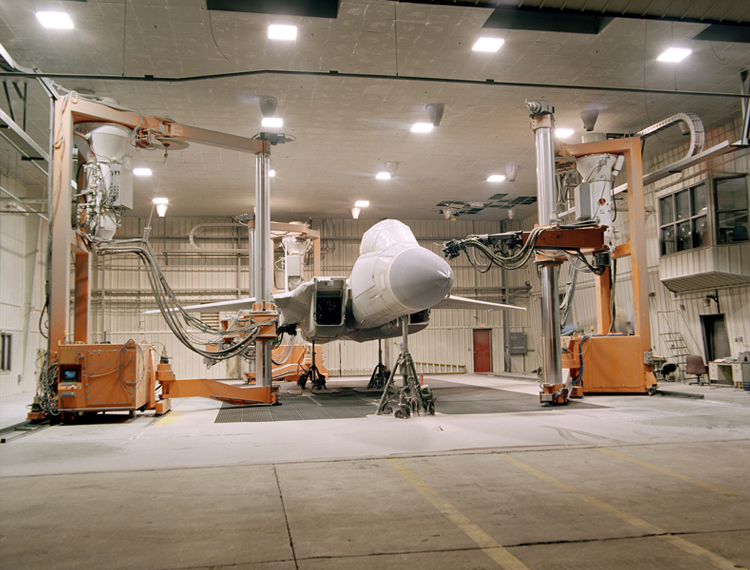
The Robotic Depaint System, operational since 1991, had two controller upgrades since 1991.
Retrofitting Industrial Robot Electronics and Software
One of the key issues in long life robotics is electronics supportability. Typically, manufacturers support robot controllers for a specific timeframe (approximately 10 years) after which new controllers must be evaluated for upgrades to extend the life of the system. The RDS system, for example, has had two controller upgrades in its thirty-year-plus life. The original solution became obsolete, and it was converted to a second controller brand after 10 years of operation, and after approximately another 10 years a third robot controller solution was necessary. When a new controller is installed any application-specific or custom-developed software and configurations will have to be ported to keep the original functionality. This may even require an industrial robot retrofit such as upgrades or rewrites to the software due to differences between the controllers, particularly if a different controller manufacturer is selected. The kinematics, or robot’s movement related to its joints, can be a key issue and require special software for the controller that cost extra. The RDS system required special kinematics when switching from the original controller to the second controller. The original kinematic solution was developed by SwRI, but could not be ported to the new controller, so the controller manufacturer developed the kinematic solution that would work for their product. Another key concern will be compatibility of path files with the new controller. It is possible that a change in controller may require path file conversion or re-generation of path files. The upgrade to a SwRI-developed “Robotic Canopy Polisher” required the path files to be retaught while the RDS required a simple conversion process to match the controller. Cables are another factor when changing controllers. Many of the cables will have to be updated to match the new controller, leading to changes in support hardware as well. Robot cables will have a recommended lifespan, and it is likely that after 10 years the cables should be replaced to maintain safety and reliability of the robot even if no other hardware changes are necessary.
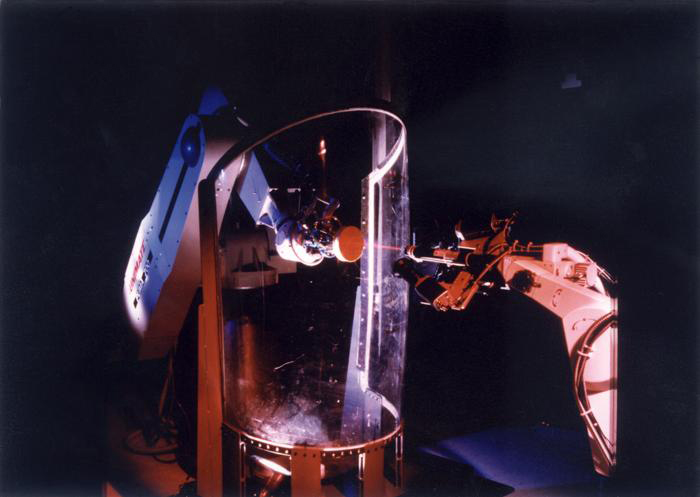
Adaptive controls were upgraded on robots used to remove scratches on aircraft canopies.
Maintaining and Modifying Motors and Gearboxes
In addition to electrical and software upgrades, after 10 years the motor and gearboxes have sufficient age and may not be supported due to obsolescence. We saw this on a project several years ago and this issue required modification to the mechanical structure to mate with the new hardware. For example, the gear reducer and motor upgrades for RDS required adaptation, since the original reducers were unavailable during the upgrade period. An alternate manufacturer, that produced a similar gear reducer, was selected. We were able to work with this new supplier to engineer and fabricate custom connections to our new interfaces.
This brings us to the topic of spare parts. If it is likely that a robot must be maintained longer than a recommended lifespan, it is important to regularly monitor availability and end-of-life dates for key components like controllers, other electronics, motors, and gearboxes so that spare parts can be purchased and stocked well ahead of a failure. Spares allow the system to continue to operate while the upgrade is being designed and planned. With these new parts and the updated interface, the system continues to operate.
Another issue of long-life robots is techniques that were used originally become obsolete and new technology or computer-controlled solutions take their place. A noticeable change over the last thirty years is brushless servo motors no longer require manual commutation setup (a person to do set up the proper phasing between the encoder/resolver and the motor). The improved motors and controllers establish the timing automatically, so the time-consuming and tedious process of establishing the phasing and timing is not required anymore. This change occurred for the RDS system when it was upgraded to a Kuka controller and the absolute resolvers were removed.
Upgrading Motion Control with Motor-Integrated Resolvers
Another significant improvement is that the absolute position of the robot no longer requires complex hardware or software. Thirty years ago, systems had to home each axis before starting operation, so the robot knew its exact position prior to any automated actions. Homing of large robots could be time consuming and require a large and open workspace. This operation had to occur after every power cycle and after certain types of faults. To get around this issue, systems used to require absolute encoders or resolvers that mechanically held their position over the full range of joint motion for each axis, so the robot always knew where it was, and therefore no homing was required.
These absolute encoders and resolvers were complex and required more physical space than the battery-backed position-management solutions of today. The images below demonstrate the difference between absolute and single resolvers.
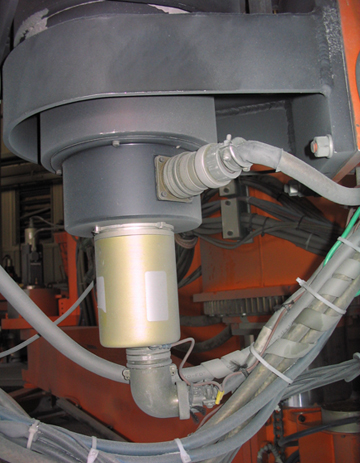
Absolute Resolver
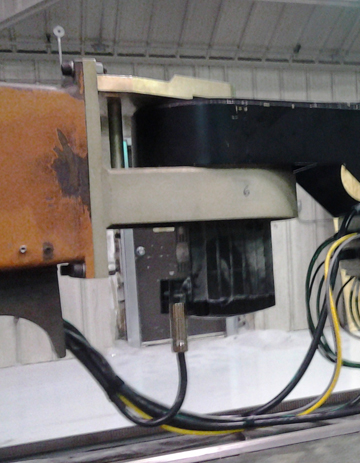
Single Resolver
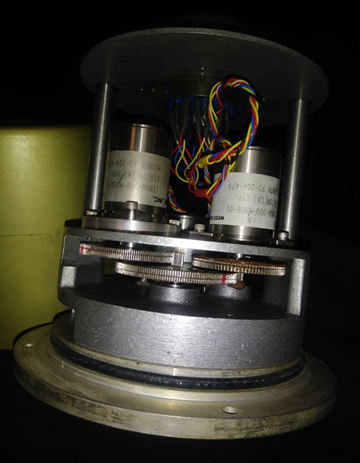
Interior of Triple Resolver
With an intentional focus on preventative maintenance, spare parts management, and careful planning for upgrades due to obsolescence, robots can operate for decades. In the case of off-the-shelf robots, an analysis should be conducted to determine whether a robot-swap is more cost effective than extending the life. Sometimes it is a close call. In the case of custom robotic systems, which are often purpose-built for an application, they should always be evaluated for service life extension. Often extending the life of a custom robot solution is the most cost-effective path forward. If you have a robotic system that is nearing the end of its lifespan, and it is critical to your operations, reach out to SwRI. Our team would be happy to review your situation.