Background
Hydrostatic test chambers are a significant part of test and simulation efforts in SwRI’s Ocean Simulation Labs (OSL). These chambers are designed to safely and reliably contain extreme pressures that simulate ocean and oilfield conditions. With a lifespan of decades, they require significant engineering efforts not only for initial design, but also for long term maintenance and monitoring. With humankind continually reaching deeper depths in the ocean and the oilfield, it is necessary to expand the OSL capabilities to perform condition simulation testing in higher pressures and larger form factors. To address this need, SwRI’s Marine Structures & Engineering (MS&E) section has teamed with the OSL to develop a new test chamber with a large bore and full ocean depth pressure rating. A key feature of this design is the development of a closure system that operates easily and quickly and an overall chamber design focused on easy operation, safety, and long fatigue life. Currently under fabrication, this chamber will increase existing capabilities while reducing the load on aging test infrastructure.
Approach
The 30-inch chamber design was performed in accordance with ASME Section VIII, Division 3 Code Requirements, SwRI internal operating procedures, and general engineering best practices. Specific attention was given to ease of chamber closure operation. Since 2010, SwRI has supplied various oil and gas customers with custom test chambers purpose-built to test individual products. Many of these customers focus on efficiency, especially concerning the ease and speed of an open/close cycle. SwRI considered design aspects of these recent projects to develop a quick-acting closure system rated for higher pressure than previous designs.
Once commissioned, this chamber will operate vertically, have a 30-inch minimum internal working diameter with an approximate 15-foot internal working length. The vessel will have a maximum allowable working pressure (MAWP) rating of 16,500 psig (considered full ocean depth) and the current design for the main body will use SA-508, Grade 4N Class 2 forgings.
The target service life of the pressure vessel will be 25+ years with a pressurization profile that includes many cycles to maximum pressure per year. Design considerations were taken to increase fatigue cycles as much as possible to reduce associated maintenance and inspection costs across the life of the chamber.
Accomplishments
The team explored several closure options and chose a design dubbed the “rook” (Figure 1) that allows for a minimal number of operator actions and only requires one piece to be lifted via crane for chamber access. The detailed design is complete and a fabrication effort started in Fall 2021. Fatigue life predictions for postulated critical crack locations are promising, as shown in Figure 2, and were obtained using models in SwRI’s NASGRO® fracture mechanics software (nasgro.swri.org), as shown in Figure 3.
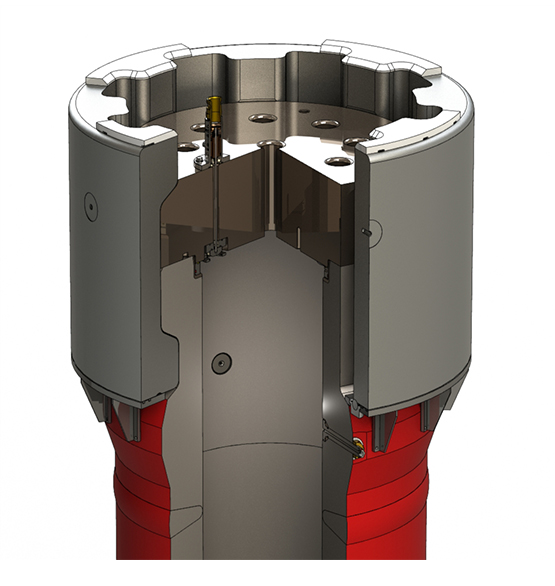
Figure 1: Final “rook” chamber closure design.
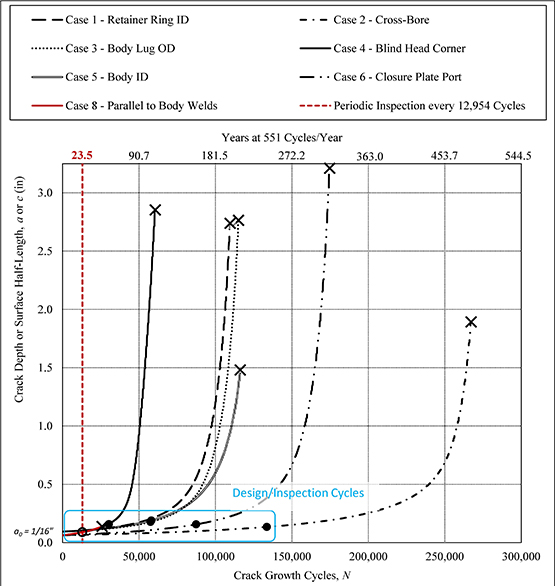
Figure 2: Postulated critical cracks and their crack growth based on anticipated pressure histogram.
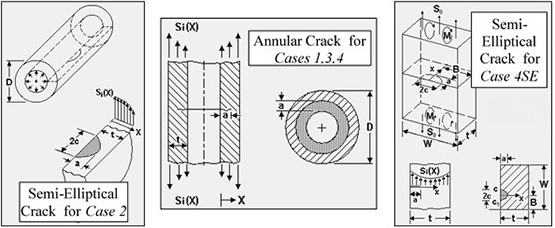
Figure 3: Postulated critical crack cases for analysis using the SwRI NASGRO® fracture mechanics software.