Background
Additively manufactured (AM) components are being adopted broadly among many industries and used in an array of applications. AM parts and structures are attractive to these industries because very complex geometries that otherwise cannot be manufactured using traditional methods can be printed and parts can be fabricated as needed. A stock of replacement parts is not required and delivery times can be significantly reduced. Two of the primary industries currently utilizing AM parts are aerospace and oil and gas (O&G). Within these industries, AM 718 is of specific interest due to the alloy’s excellent mechanical properties over a wide range of service temperatures. Several companies in the aerospace sector are currently exploring the feasibility of AM parts in rocket propulsion systems, and others have already used AM to fabricate critical rocket components. Guidelines are currently being developed in the O&G industry for the qualification and certification of AM parts for offshore applications. However, in many of these applications alloy 718 is susceptible to hydrogen embrittlement (HE). Microstructural characterization and mechanical properties of AM Alloy 718 are reported in the literature, but the performance of AM 718 in gaseous hydrogen environments has not been thoroughly investigated.
Approach
To understand the underlying mechanisms governing the susceptibility of AM alloy 718 to HE under HPHT conditions, mechanical testing, metallurgical evaluations, and hydrogen-alloy interaction experiments were completed on wrought material and three different AM build configurations. Mechanical testing was performed on wrought and AM test specimens in high-pressure gaseous hydrogen to determine the fatigue crack growth rates. Detailed microstructural evaluations were completed to understand the effects of AM parameters and post-build thermal processing parameters on the porosity, grain size, phase constituents, and hardness. Hydrogen-alloy interactions will be characterized using Thermal Desorption Spectroscopy (TDS) and Scanning Kelvin Probe Force Microscopy (SKPFM) by UTSA. TDS will be utilized to determine the hydrogen binding energies and total concentrations within the materials, and SKPFM will be utilized to spatially resolve atomic hydrogen within the metallurgical features of the various alloy configurations.
Accomplishments
The mechanical testing in high pressure hydrogen gas was completed and demonstrated a significant effect from hydrogen. The crack growth rates in gaseous hydrogen environment increased dramatically, and when employed in damage tolerant structure, these hydrogen effects will dramatically reduce the lifetime of components. Post-test characterization of the fracture surfaces revealed a distinct change in fracture mode for all material types from lab ambient condition to high pressure gaseous hydrogen: a transgranular fracture mode in air and an intergranular mode in hydrogen. The metallographic evaluations revealed significant variations in microstructure between the wrought and AM materials. The wrought microstructure has a clearly defined grain structure with expected annealing twins. Two of the three AM material configurations contained regions with cellular morphology consistent with remnant columnar structures that were not recrystallized upon solidification of the AM laser melt pool. These features are artifacts of the AM build process and post-process thermal treatment. Upon completion of the mechanical testing, fracture surface examination, and metallurgical examinations, no unique metric was established to determine the severity of hydrogen embrittlement for the wrought and AM alloys.
Additionally, the total hydrogen concentrations, the internal distributions of hydrogen, and the binding energies of hydrogen populations will be used to understand how the microstructure affects these material properties upon completion by UTSA.
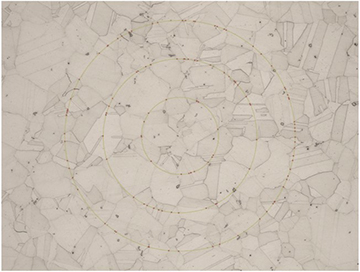
Figure 1: Microstructure of wrought Alloy 718.
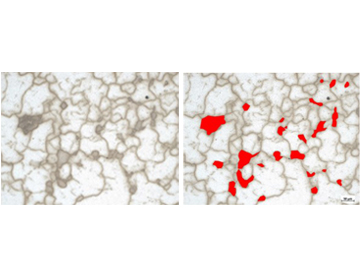
Figure 2: (a) Microstructure of AM Alloy 718 and (b) remnant columnar structures in RED from the AM and post-build thermal processes.
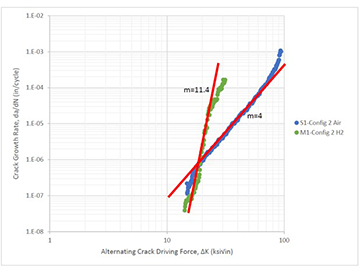
Figure 3: Dramatic increase in fatigue crack growth rates were measured in the wrought and AM materials. In this figure, the increase in crack growth rate for AM configuration 2 is presented.