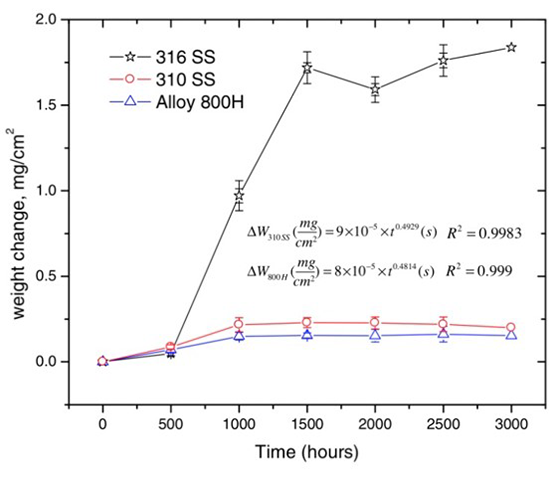
Figure 1: Weight gain of three alloys after exposure to sCO2 (650°C and 20 MPa) at 500 hours interval.
Background
The annual worldwide cost of corrosion, due to prevention, mitigation, and repair, has been reported to be over $5 trillion. To address climate change and energy needs, technologies are improved or developed requiring higher pressure and temperature (HPHT). Therefore, materials degradations must be better understood in those extreme environments (e.g. supercritical CO2 or deep oil and gas wells.) Since environmental degradation is not linearly proportional to time (as shown in Figure 1), the reliability of life prediction can be improved by obtaining more data. In-situ techniques help greatly reduce the cost per data point and increase the quantity of data. However, very few in-situ corrosion HPHT techniques exist. The objective of this project was to use ellipsometry to accurately measure oxide film thickness growth in-situ in HPHT environment.
Approach
Ellipsometry is an optical technique where the light from a laser is reflected off the specimen surface into a sensor to measure polarization change. Oxide thickness evolution from nm to µm can be derived from changes in polarization phase and amplitude measured at regular intervals. This technique has never been used at HPHT. A single wavelength ellipsometer was added to an autoclave used to expose various metallic alloys to sCO2. The hardware was kept outside of the harsh environment, as the laser passed through HPHT windows, to make this a cost effective in-situ technique.
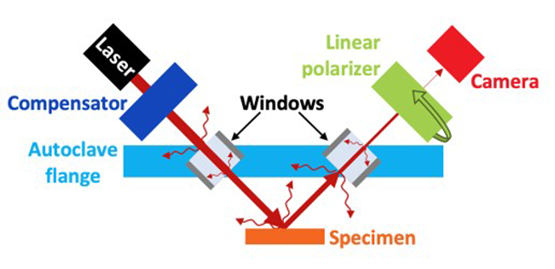
Figure 2: Schematic representing the degrading of the laser signal going through the in-situ ellipsometer.
Accomplishments
An ellipsometer was successfully added to an autoclave to measure oxide film formation in situ. The standalone ellipsometer could measure a 100 nm thick deposited oxide with a 3% accuracy when compared to SEM measurements. HPHT sCO2 and sour upstream environments were safely replicated in the dedicated autoclave. A software tool was developed to automate data collection and analysis. Using this tool, it was possible to gather data at hourly intervals and less without the user being present and to reduce the analysis time from one week to less than one hour.
The thicknesses obtained using the ellipsometer in situ were 1,000 times higher than the actual oxide (measured using SEM). This resulted from a degrading laser signal as it passes through the polarizers, the autoclave window, and any gas/liquid interfaces (as represented in Figure 2). This led to poor fits of the data used to calculate the thickness. This systematic error was only identified after analyzing all the data collected, once the software tool was developed late during this project. It is hypothesized that better quality data can be obtained with a more powerful laser.