Background
Leveraging an existing compressor test loop and prototype, the Mechanical Engineering Division is expanding its reach into reciprocating compressor machinery design and development. Hermetically-sealed compressors are becoming more important as hydrogen and hazardous gas applications continue to grow. The development of key components of a hermetically sealed compressor makes safe, efficient, and reliable compression of hazardous gases accessible to a much wider range of consumers. Currently, the state of the art for hydrogen compressors is not sufficiently reliable or efficient. Through this IR&D project, SwRI is leveraging its role of a leader of hermetically sealed compressor technologies and linear actuated reciprocating technology in order to be able to advance novel, more reliable, and more efficient compressor technology.
Approach
The research objectives were accomplished by advancing technology in the following areas:
- Magnet Coatings – Developed a coating and process method that will protect magnets from hydrogen incursion, diffusion through its lattice, and embrittlement due to metal hydride formation, leading to mechanical failure.
- Valve Design – Developed an improved compressor cylinder valve design with minimal leakage for hydrogen service.
- Dynamic Seal Incorporation – Installed and tested a novel, custom dynamic ceramic-on-ceramic seal.
- Motion Profiles – Developed and tested an improved and more ideal compressor motion profile.
Each of the above-noted technologies were tested in the existing compressor test loop and prototype hermetically-sealed linear motor driven reciprocating compressor.
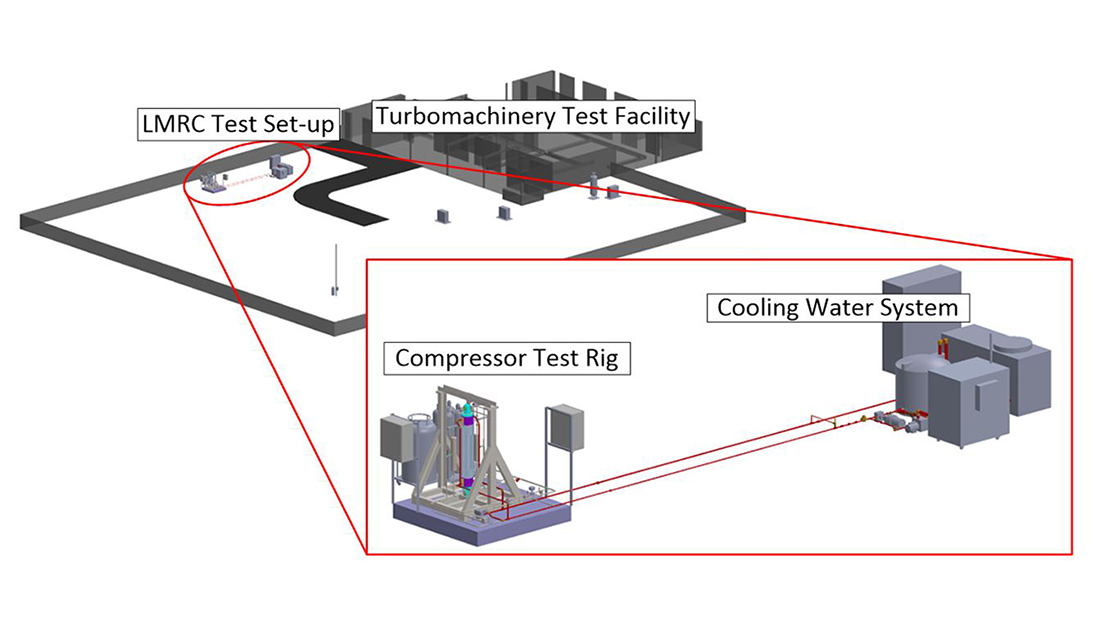
Figure 1: Concept Image of Existing SwRI Hydrogen Compressor Test Loop.
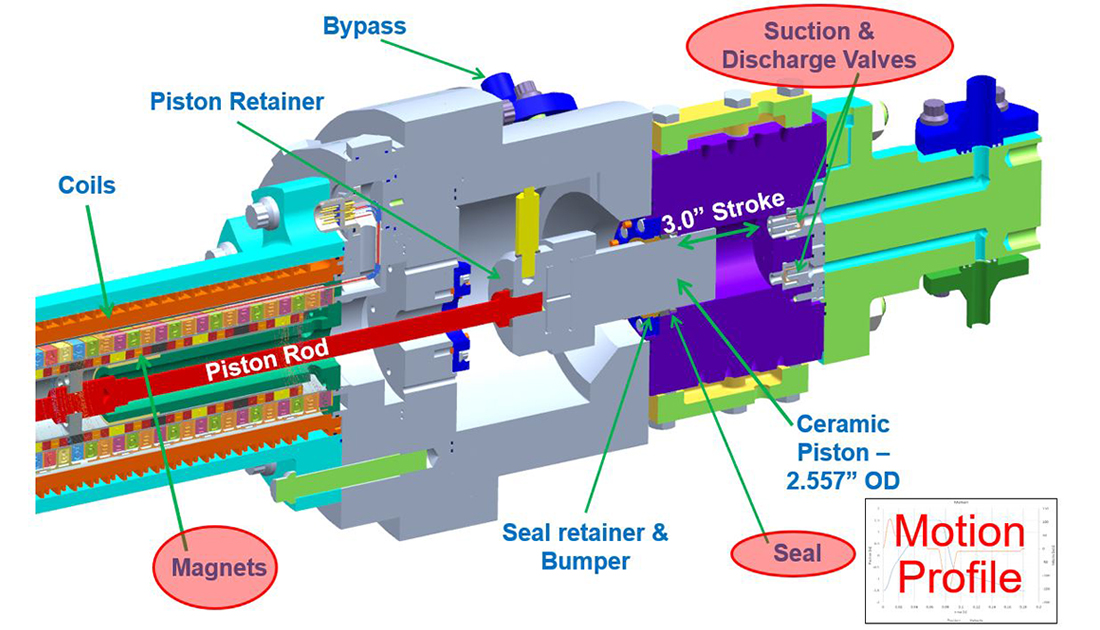
Figure 2: Four Technologies Developed and Tested in the SwRI Test Loop and Prototype Compressor.
Accomplishments
A standard nickel magnet coating with specified thicknesses of each layer was found to allow magnets to survive a pressurized hydrogen environment for at least 21 pressure cycles of hydrogen, which amounted to approximately 711 hours in pressurized hydrogen.
Compressor valve designs were analyzed using CFD and modified to improve aerodynamics and overall losses, as well as making their assembly more reliable.
When testing the new valves and novel ceramic-on-ceramic dynamic seal, compression was achieved, but leakage across the seal resulted an inefficient process. Testing with the new valves and polymeric dynamic seal resulted in a better flow efficiency.
Because of the linear actuator design, which does not force the mechanical motion of the piston to a fixed profile, it is possible to test a range of motion profiles. In the tests performed, the profile of a conventional reciprocating compressor was compared against a newly developed motion profile that attempted to optimize the compression efficiency. The conventional profile was observed to have an isentropic compression efficiency of approximately 92.3%, whereas the optimized profile was calculated to have a 96.3% efficiency. This 4 percentage-point increase to efficiency is considered to be a significant improvement to existing reciprocating compressor technology that has been developed and improved upon for the past seven or more decades.
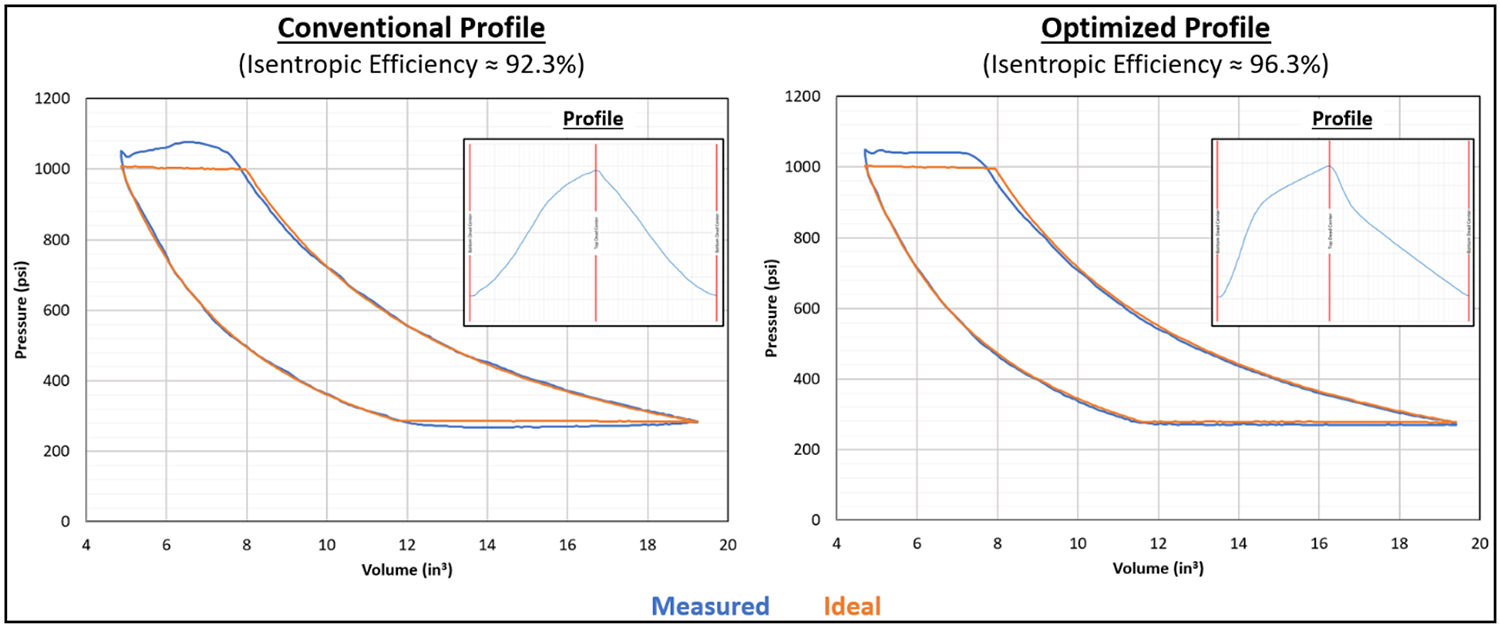
Figure 3: Measured Pressure Volume Plots for Conventional Compressor Motion Profile and Optimized Motion Profile.