Background
Electrification provides an important path for greenhouse gas reduction in personal mobility but is much less viable in most freight transport applications. The combination of long distances, high load factors, and powertrain lifecycle costs results in ongoing client interest in internal combustion engines with improved freight movement efficiency and greenhouse gas reduction. Natural gas engines offer an attractive technology path and there is growing worldwide interest in the further development of natural gas-powered heavy-duty vehicles. To date the efficiency of natural gas engines has been hindered by their development as derivatives from diesel truck engines. A previous Exploratory Internal Research project (03-R6155) demonstrated a promising path toward improved efficiency of diesel-derivative natural gas engines. Patent application is in progress but an integrated combustion system and its benefits versus higher-cost approaches needs further quantification to generate client interest and project investment.
Approach
Two natural gas combustion systems at two different cost points are being designed and demonstrated through computational analysis. The lower cost point system uses a diesel derivative cylinder head and minimal further engine redesign but incorporates SwRI intellectual property and further technologies previously demonstrated on other spark-ignition engines – dual sparkplugs, direct fuel injection, and enhanced surface temperature control. The higher cost point system incorporates the same technologies using a dedicated pent-roof natural gas cylinder head and new valve train. Both systems contain SwRI intellectual property that can be offered in royalty-free licenses in exchange for engine development projects. Quantified efficiency projections for each combustion system are being prepared for cost / benefit evaluation.
Accomplishments
The project is currently just past its midpoint. The two combustion systems have been developed with cylinder head configurations as shown in Figure 1. Each combustion system uses direct injection of natural gas into the center of the combustion chamber, with two sparkplugs placed as shown in the figures. The far-square tumble port system allows the features to be incorporated in a diesel engine with minimal modification. It utilizes a SwRI-designed intake port arrangement for which a patent application has been filed. The pent-roof design is a higher cost point solution that is expected to provide optimal performance.
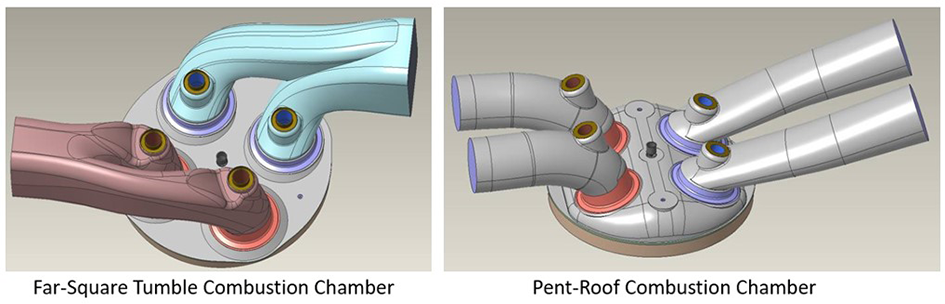
Initial data is summarized in Figure 2, where Turbulent Kinetic Energy (TKE) is plotted versus crank angle through the end of the compression process. Efficiency is enhanced by increasing the TKE at the point in time when the sparkplugs ignite the reactant mixture. For comparison purpose, the baseline case shown with the red curves through several engine cycles is indicated. Design 1 in the plot is the SwRI far-square tumble system. The green lines are the initial results. Some improvement was seen but it was then found that fuel injection timing was as important variable. Advancing the Start of Injection (SOI) resulted in a significant increase in TKE throughout the time period in which the sparkplug would be ignited (-25 to -5 Crank Angle Degrees (CAD)).
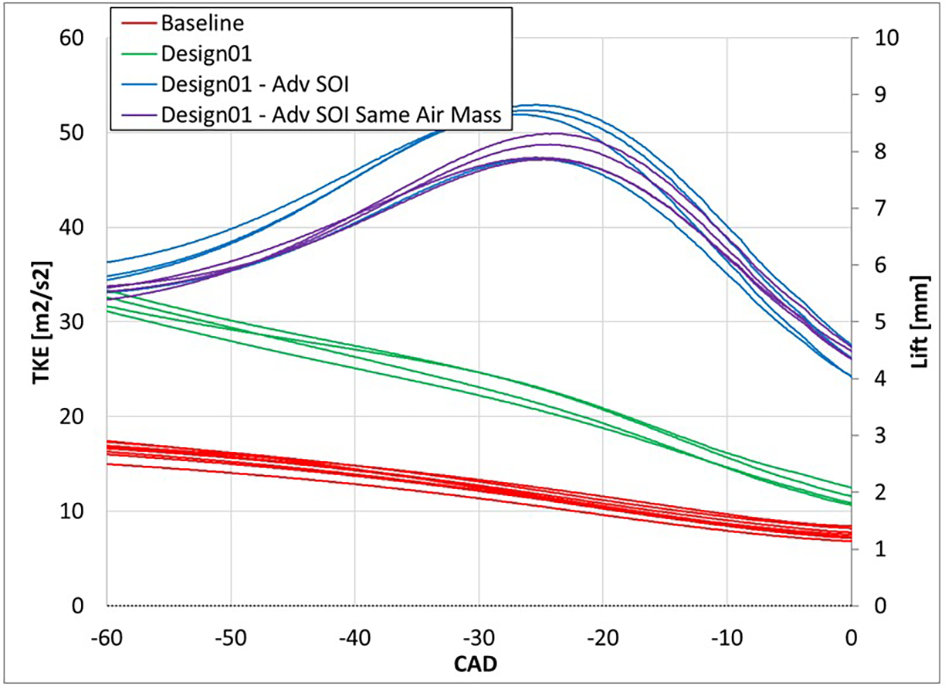
Analysis continues with the assessment of how much the increased TKE will improve thermal efficiency. The cases shown here will then be compared with the higher cost point pent-roof system. The results will provide a detailed picture of costs versus benefits an engine company could take in developing state-of-the-art heavy-duty natural gas engines.