Background
As electric vehicles become more common, the industry is learning more about the unique requirements of the lubricants for these vehicles. One concern is that the inverters that change the DC battery power to AC for the motor can cause current leakage within the driveline. This can cause current to flow through the lubricant. How this affects the friction and wear is not well-understood, and, to date, very few rigs have been adapted to allow for electric current to be applied while testing.
Approach
Two of the tribology test rigs (tribometers) are particularly valid for electric vehicle drivetrain studies. These are the mini traction machine (MTM) and the bearing tester (ARKL). The MTM allows the ball and disc (test samples) to be rotated at different speeds to each other, thereby introducing a slide roll ratio. This can replicate what happens in a gearbox as the teeth are meshing. The ARKL test specimen is a deep groove ball bearing thrust washer and can be used to study the effect of current flow through a bearing and race. Using techniques developed during a previous IR where we electrified a block on ring test rig, both the MTM and ARKL will be electrified.
Accomplishments
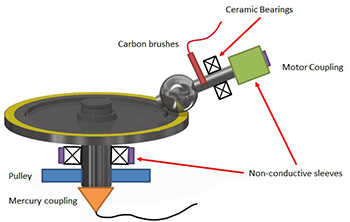
Figure 1: Schematic of electrified Mini Traction Machine.
The MTM has been electrified as shown schematically in Figure 1 and much of the test matrix completed. The ARKL designs for electrification have been completed and will be the focus of the remaining time. It has been observed that the wear increases when AC or DC current is applied across the test samples. A U.S. patent application was filed on 05/16/2023: 63/502,515, “Apparatus and Method to Evaluate the Effect of Electrical Potential Between Moving Surfaces.”