Background
There has been significant success with the development and demonstration of MW-scale supercritical CO2 power systems at SwRI. At the same time, kW-scale power generation has been largely confined to less-efficient organic Rankine cycle technology. Using a supercritical CO2 closed Brayton cycle as shown in Figure 1 can provide a dramatic increase in the efficiency of small scale thermal power systems.
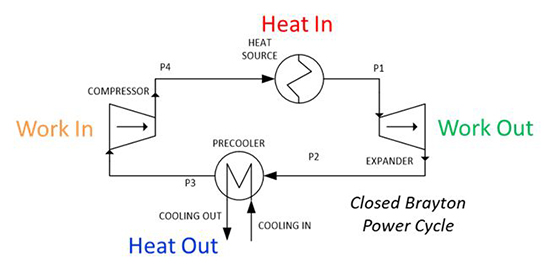
Figure 1: Closed Supercritical CO2 Brayton Cycle
The technical challenge is the power density of supercritical CO2 power cycles; expander technology has been developed for turbomachinery that is effective at the MW-scale, but no developed expander technology exists for a kW-scale system. Successful development of the expander (and compressor) machinery for a system of around 30 kW power output would be a significant improvement for mobile waste heat recovery systems (under development for on-highway heavy-duty trucks) and stationary systems (industrial and commercial waste heat recovery, remote power generation, and so on).
APPROACH
The project has proceeded in three linked stages: (1) thermodynamic cycle analysis, (2) component evaluations, and (3) machinery concept design. The thermodynamic cycle analysis has considered a heavy-duty truck application, with waste heat taken from the exhaust gas recirculation and/or exhaust systems. This analysis has shown the potential benefits of supercritical CO2 waste heat recovery on heavy-duty truck efficiency as a representative application. The component evaluations have evaluated turbomachinery and piston machines as possible compressor/expander technologies. The concept design will generate both an overall system layout and expander machine initial designs, with callouts to areas where significant technology development will be required before a practical machine can be constructed.
ACCOMPLISHMENTS
Thermodynamic cycle simulations have shown that a power cycle efficiency of 30 percent can be achieved using engine exhaust as the heat source. The cycle efficiency is highly sensitive to the low-side temperature at the inlet of the compressor; the results of the simulations show that the temperature at this point must be close to ambient conditions for maximum cycle efficiency. Transferring this performance to a heavy-duty truck suggests that, depending on the speed-load point the engine is operating at, a 2-6 percent improvement in fuel efficiency can be achieved with the addition of a supercritical CO2 waste heat recovery cycle (a speed-load map of efficiency improvements is shown in Figure 2). Ongoing work is determining the potential performance of individual components within the power cycle to validate the efficiency improvements predicted to date.
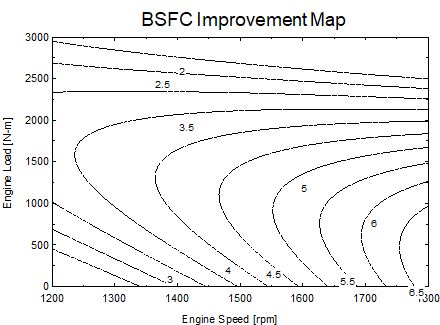
Figure 2: Efficiency Gain from Supercritical CO2 Waste Heat Recovery on a Heavy-Duty Truck Engine