From 1752, when Ben Franklin used a key attached to a kite to collect electricity from lightning, to 1882 when Thomas Edison opened the first central electric power plant more than 100 years later, tremendous progress was made in the field of electricity. Edison’s Pearl Street Station in lower Manhattan used boilers to heat water for the high-speed steam engines that powered electricity-generating dynamos. There have been many, many advances since, but one thing has remained largely the same: Most electrical power is generated with steam.
DETAIL
A watt is a unit of power that quantifies the rate of energy transfer. A megawatt (MW) is equal to one million watts.
For the past decade, Southwest Research Institute has been at the forefront of researching new power cycles to replace steam with supercritical carbon dioxide (sCO2) as the working fluid. Component development efforts for commercializing these power cycles have progressed rapidly in recent years, and the technology is poised for demonstration at a 10 MWe scale at the Supercritical Transformational Electric Power (STEP) pilot plant at SwRI. These power cycles could revolutionize power generation, improving the cost, efficiency and responsiveness of electricity production to changes in demand.
ABOUT THE AUTHORS
Dr. Aaron McClung (left) manages SwRI’s Power Cycles Machinery Section and is the principal investigator and technical lead of the STEP demonstration pilot plant, pictured in the background. He’s holding a model of a revolutionary desk-sized 10 MWe sCO2 turbine that could power 10,000 homes. Dr. Tim Allison directs the Machinery Department in SwRI’s Mechanical Engineering Division. His development and test experience includes new turbomachinery technologies, such as novel sCO2 turbines and compressors, a high-pressure oxy-fuel combustor and a high-temperature gas turbine recuperator.
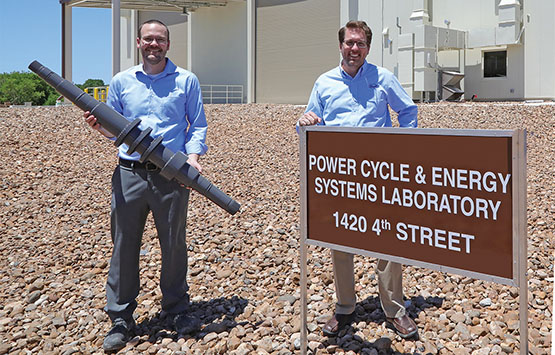
SCO2 POWER CYCLES
Most power plants in the United States today are more than 30 years old and operate below 35% efficiency. About 60% of all power in North America comes from fossil fuels, so these inefficient plants burn huge quantities of expensive hydrocarbon fuels and emit significant amounts of greenhouse gases. Alternative energy sources such as wind, solar and hydropower are making impressive inroads in the power generation spectrum but face challenges associated with variable production and storage. Even with continued improvements in alternative energy technology, a diverse portfolio of electricity-generating plants, with many utilizing fossil fuels, will almost certainly be required for many years. If the U.S. continues to rely on fossil fuels, it is imperative to increase plant efficiency while also decreasing emissions produced.
Supercritical carbon dioxide power cycle technologies that use high pressure CO2 as a working fluid can increase power plant efficiency by as much as 10% relative to steam cycles. Carbon dioxide typically behaves as a gas at ambient temperatures and pressures, or as a solid — dry ice — when frozen. When held at temperature and pressure above its critical point (1,070 psi, 88° F), CO2 acts like a gas while having density near that of a liquid. It’s also nontoxic and nonflammable.
The anticipated economic and environmental benefits of sCO2 power plants include higher efficiency, reduced fuel consumption and lower emissions with decreased cooling water consumption. Additionally, the compact design and small footprint of sCO2 turbomachinery technology would lower capital costs and improve ramp rate capabilities that are becoming more important as additional renewable energy resources are brought online. Power plants can be designed using sCO2 cycle technology to use heat from gas turbine exhaust, fossil fuel combustion, solar thermal, geothermal or even nuclear sources. Some direct-fired variations are directly heated through high-pressure oxy-combustion of natural gas.
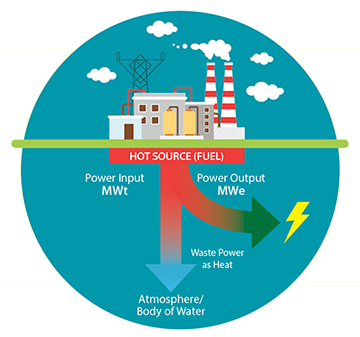
Powerplants are assigned two values: megawatts electric (MWe) and megawatts thermal (MWt). The former refers to the output capacity of a power plant, while the latter refers to the input thermal energy required. For example, a coal-fired power plant rated at 1,000 MWe and 3,000 MWt will require 3,000 MW of heat from burning coal for every 1,000 MW of electricity produced. Typical older power plants are rated 1,000 MWe/3,000 MWt, which translates to an efficiency of 33%. The closer a power plant’s MWt and MWe ratings are, the more efficient it is.
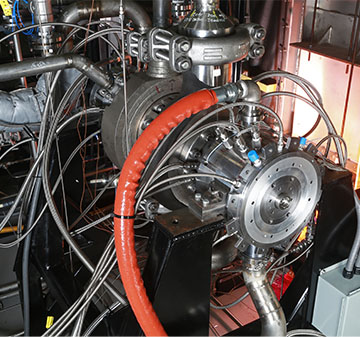
SwRI successfully operated this 10 MWe scale sCO2 expander at up to 1,320° F and 3,600 psi, proving its ability to withstand the sCO2 operating environment.
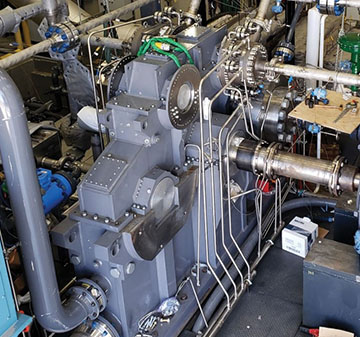
Engineers are testing an integrally geared compressor-expander prototype for its performance and durability.
While concepts for sCO2 cycles date back to the 1960s, recent advancements in heat exchangers and turbomachinery components are now bringing the promise of its potential to fruition. These sCO2 systems operate at high fluid density at turbomachinery inlet and exit conditions, enabling efficient compression and extremely power-dense turbomachinery and heat exchangers. The thermodynamic properties of sCO2 offer better cycle efficiency than steam cycles, particularly at low ambient temperatures and at turbine inlet temperatures exceeding 1,000– 1,100° F. The compact system packaging, fast startup capability and high-power density of sCO2 allow for modular and efficient power generation, all with an inert fluid.
DETAIL
Closed power cycles use a fixed mass or “charge” of working fluid in the system to drive a turbine and create energy, recirculating the fluid from the turbine exit instead of emitting it into the atmosphere. The working fluid is cooled and recirculated for continuous operation of the system. A recuperated power cycle adds a heat exchanger between the turbine and the cooler to transfer thermal energy to the cold, high-pressure stream entering the primary heater, minimizing heat input into the cycle and increasing thermodynamic efficiency.
In recent years, sCO2 research programs have targeted specific component- and system-level technology gaps motivating the development, construction and operation of multiple MW-scale test loops. SwRI and our collaborators have developed, prototyped and validated multiple compressor and turbine designs. Notable recent successes include operating a 10 MWe axial expander prototype up to 1,320° F and 3,600 psi. This axial-flow turbine expands high-pressure gas to drive a compressor or generator. SwRI is also testing an integrally geared compressor-expander prototype. This relatively low-cost, multi-shaft turbomachine enables compressor impellers and turbine wheels to operate at the optimum speed for every stage, resulting in higher efficiency than most turbomachinery.
Research projects targeted specifically at gas turbine waste heat recovery (WHR) systems are underway. These systems use a heat exchanger to extract high-temperature waste heat from a gas turbine exhaust stream and convert this thermal energy to power using an sCO2 cycle, increasing the overall system efficiency as a combined cycle. The team is adapting high-temperature machinery designs to lower-temperature WHR operations while developing mature technoeconomic models for designs that operate over a range of ambient temperatures and load profiles. Combined cycle analysis results show that plant efficiencies near 50% are achievable even for small-scale 20 MWe systems with no changes to the gas turbine — efficiencies well above conventional open-cycle gas turbines. This increase in power output by converting waste heat to power inherently lowers emissions and increases system efficiency.
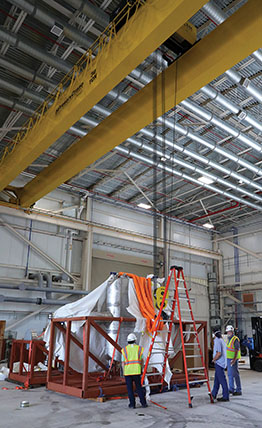
Component manufacturing and equipment installation begins in the STEP facility, aided by a ceiling-mounted 30-ton crane.
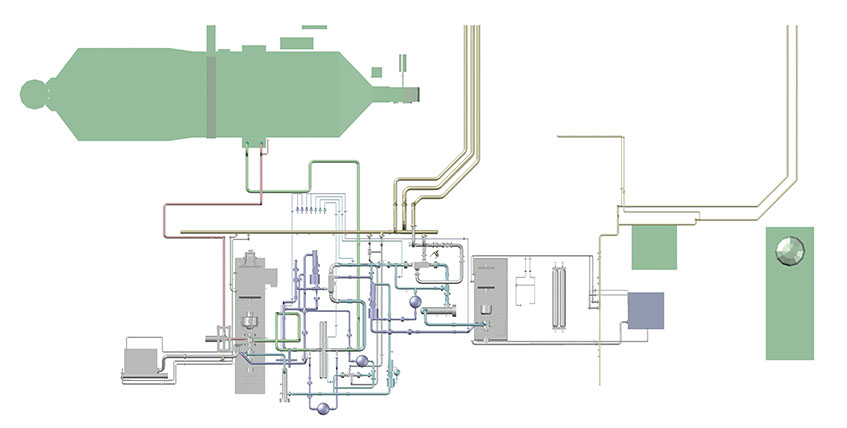
SwRI has entered the equipment installation phase for the STEP pilot plant, shown in this layout with the turbine skid at left and the compressor skid at right. The sCO2 heater is the large green element at top.
Advanced Components, Technologies
SwRI, the Gas Technology Institute and General Electric are advancing sCO2 technology, designing, constructing and operating a pilot plant test facility to demonstrate sCO2 power cycle technologies at a commercially relevant scale. STEP is a state-of-the-art facility valued at $124 million with primary funding provided by the Department of Energy along with cost sharing from industry partners and the state of Texas. This pilot plant will advance sCO2 technologies to near-commercial readiness, demonstrate their operability and performance, and serve as a reconfigurable test facility for component development and validation now and in the future.
DETAIL
Recuperators recover thermal energy from the turbine exhaust and use it to preheat the working fluid entering the primary CO2 heater, minimizing heat rejection and improving thermal efficiency.
The STEP pilot plant is a significant scale-up from existing sCO2 test loops. Designed as a fully integrated and functional electric power plant, the 10 MWe facility supports operation at sCO2 turbine inlet temperatures up to 1,320° F. This demonstration project mitigates technical risks and challenges for key components including the turbomachinery, recuperators and materials. The facility will demonstrate the aerodynamics, sealing performance and durability of full-sized turbomachinery for sCO2 power cycles scalable to 100s of MW. The pilot plant will also prove the performance, fabrication and durability of compact heat exchanger designs. The project sources materials for large-scale hardware to verify the corrosion, creep and fatigue characteristics of these materials in high-temperature CO2. Finally, the project will demonstrate successful integration and operability of all system components through many ambient conditions and operating states, including startup, transient and shutdown.
Next Steps
The 22,000-square-foot laboratory building housing the pilot plant was recently completed on a five-acre site at SwRI’s headquarters in San Antonio. The facility will feature skid-mounted components that provide flexibility and a unique reconfigurable design, which allows it to evolve over time to keep pace with industry advancements. The plant is also home to external heating elements and a cooling tower, a separate electronics room and a 30-ton crane that will support the project operation and construction of the sCO2 power block.
Now that the building is completed, component manufacturing and equipment installation is progressing, with the aim of starting operations in 2021. Comprehensive testing to evaluate the advancement of sCO2 technology will follow. State-of-the-art equipment is being developed by STEP partners, including a revolutionary desk-sized 10 MW sCO2 turbine that could power 10,000 homes.
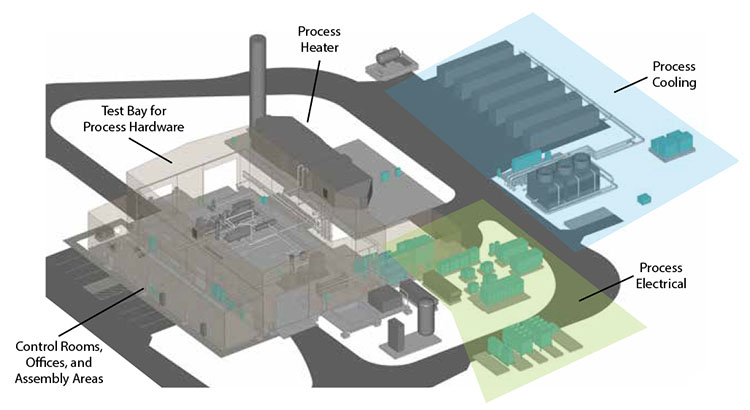
The 22,000-squarefoot pilot plant building was recently completed on a five-acre site at SwRI’s headquarters in San Antonio. The overall facility includes external heating elements, a cooling tower and a separate electronics room.
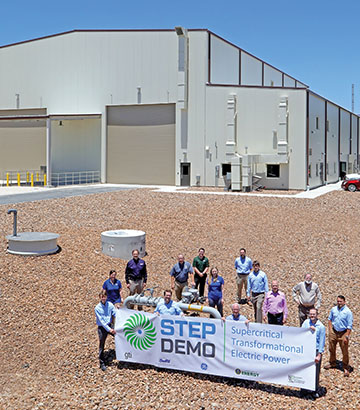
Team leaders for the construction of the Supercritical Transformational Electric Power pilot plant building include C.J. Nolen, Katie McLoud, Eric Thompson, Dr. Tim Allison, Dr. Jeff Moore, Brittany Tom, Josh Neveu, Danny Deffenbaugh, Stefan Cich, Scott MacAdam of GTI, Jon Wade, Al Steiner, Dr. Aaron McClung and Trenton Cook. The 22,000-square-foot building was completed in June after 18 months of construction. The pilot plant facility is expected to be operational in the fall of 2021.
Optimus Industries LLC is providing the primary process heater, incorporating a ~80 MWt gas-fired burner and heat recovery steam-generator-style CO2 heater fabricated from superalloys for operation up to 1,320° F. The 16 MW (gross) axial turbine, developed jointly by SwRI and GE, has a 100,000-hour commercial product design life at inlet conditions of 1,320° F and 3,626 psi. The team is also procuring rotor and casing materials and initiating fabrication.
High- and low-temperature recuperators include compact printed circuit heat exchangers. Photochemically etched fluid channels provide numerous microchannels with exceptionally high thermal performance, while diffusion bonding produces a solid core packed within a heat transfer area. The combined result is maximum efficiency and minimum footprint, ensuring the lowest total life cycle cost.
Collaborator Baker Hughes is providing a pair of 3 MW gas compressors. GE has developed the turbine control/stop valve based on its existing commercial product line of steam valves. However, the STEP valves were modified from a design for advanced ultrasupercritical steam power plants to accommodate high operating temperatures and pressures for the sCO2 system.
The facility includes high-temperature piping designed to ASME B31.1 code and fabricated with corrosion-resistant alloys well suited for service in extreme environments. Additional plant equipment includes low-temperature piping, cooling towers, coolers and valves as well as CO2 supply and inventory control systems.
STEP DEMO
The team will initially test a simple recuperated cycle architecture. A second round of testing for a higher-temperature recompression cycle configuration will follow. Once these initial phases are complete, the reconfigurable facility can be adapted to perform validation testing of alternative component designs, cycle layouts or control logic. The system may also be extended to include additional components (such as thermal energy storage, oxycombustion hardware) or to perform validation/qualification testing of full-scale waste heat recovery systems.
The STEP plant will demonstrate technology that could revolutionize the power plant industry. The high overall density of sCO2 as a working fluid allows turbomachinery to be approximately one-tenth the size of conventional power plant components, providing the opportunity to shrink the environmental footprint and construction costs of new facilities. The technology can also use industrial waste heat, concentrating solar power or practically any other heat input to generate electricity. Like Franklin and Edison in their time, the STEP team is working toward the next generation of higher-efficiency, lower-cost electric power technology.
Questions about Supercritical Carbon Dioxide Power Systems? Contact Dr. Tim Allison or call +1 210 522 3561.