Aircraft fleets around the world regularly continue flying far beyond their intended service life and frequently operate in more severe environments than their airframes were designed to withstand. Ensuring that both military and commercial aircraft fleets remain operational and flightworthy is a crucial component of our nation’s defense and air travel systems.
To extend airframe life requires an understanding of aging designs, identifying critical structures prone to wear or failure, and inspecting those structures regularly. And as costly and challenging as that is, electronics, avionics and weapons systems also must be kept current to operate in an increasingly information-intensive environment. Military fleets, some of whose aircraft were designed in the 1950s and ‘60s, must deal with complications such as suppliers who have gone out of business and components that have become obsolete. Meanwhile, weapons and navigation systems must be updated to defend against the modern threat environment, and cockpit electronics must be adapted to enhance situational awareness.
Southwest Research Institute’s military aircraft life-extension work has included avionics support to keep the A-10, B-1, B-52, F-15, F-16, F-22 and T-38 planes as well as rotary wing aircraft in service and still flying with cutting-edge capability. Commercial and space systems also are supported by SwRI-developed and -supported software tools, including several that determine how cracks grow and engines perform over a lifetime of service. We have decades of experience in this area, and in 2020 and early 2021 we received several new contracts supporting aircraft life extension. One of these is a six-year indefinite delivery, indefinite quantity (IDIQ) contract to support the U.S. Air Force Academy Center for Aircraft Structural Life Extension (CAStLE) to study the effects of aging on military aircraft. Others include multiyear redesign and modernization efforts retrofitting and sustaining several critical subsystems on the F-16, A-10 and B-1.
We have addressed these tasks and others through a multidisciplinary, multidivisional approach that stresses the “5 Ms” — measurement, modeling, monitoring, maintenance and modernization.
Measurement
Aging aircraft face potentially serious structural problems, including material fatigue, where cyclic loads or stresses experienced during takeoff, flight and landing can initiate and propagate cracking. Once a crack starts, it will grow a small amount with each subsequent loading cycle, until the component fails. For decades, SwRI engineers have worked with the U.S. military to develop structural integrity programs that use testing, measurement and analysis to ensure that an aircraft structure will operate as intended. This process provides information for fleet-management decisions, such as creating inspection and maintenance plans and setting modification priorities. SwRI maintains extensive facilities to measure the mechanical and physical properties of all types of structures and materials, supporting static, dynamic and fatigue tests on components, subassemblies and full-scale test articles.
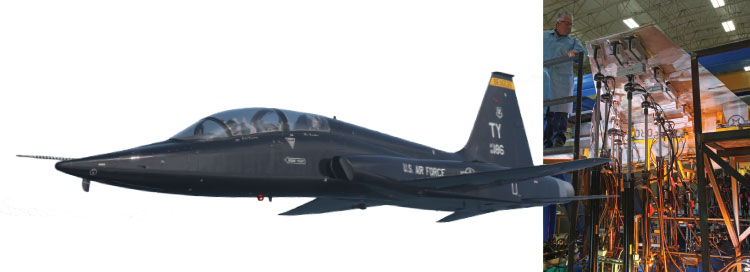
Courtesy of USAF Master Sgt. Burt Traynor
Since the 1960s, the Air Force has structurally modified the fuselage of its advanced flight trainer, the T-38 aircraft, to extend its structural life. SwRI conducted a full-scale structural fatigue test, destructive teardown and economic life evaluation to help assess remaining life and identify potential fatigue-critical locations.
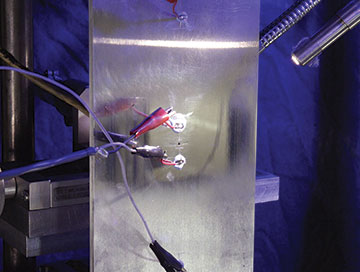
Holes are drilled in a material test sample to replicate fatigue-critical locations. The sample is then instrumented and subjected to various loads to study crack growth.
Over the last several decades we have developed techniques to evaluate the structural integrity of military aircraft such as the A-10 Thunderbolt II and the T-38 Talon, developing testing and measurement methods to determine how often aircraft and components need to be inspected for flight safety. In some cases, we have developed fatigue and crack growth data using small samples, or coupons, of the materials used to make major structures. Controlled testing of aircraft materials reveals how cracks originate and determines how quickly they grow. Other times we use full-scale test setups to recreate the loads experienced in flight and collect stress data using an array of strain gauges.
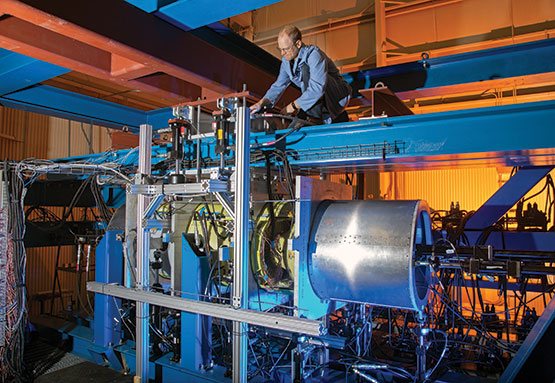
This complex custom test stand evaluates the structural integrity of next-generation jammer pods under real-world conditions. The pods are installed on EA-18G Growler aircraft to thwart enemy radar and targeting systems.
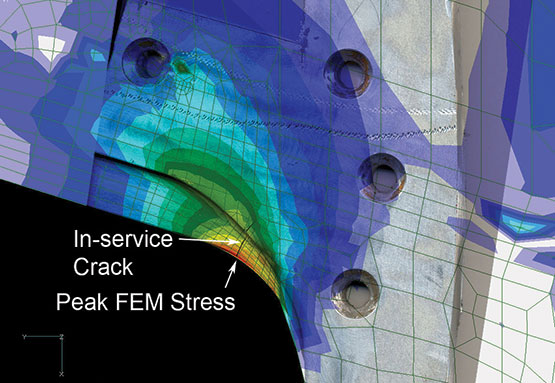
Using finite element analysis, SwRI analyzes stress in airframes and components to develop appropriate inspection and maintenance schedules.
We also help sustain critical systems through the USAF Aircraft Structural Integrity Program’s Comprehensive Landing Gear Integrity Program. These systems contain hundreds of parts and perform a vital function. A “belly landing” due to landing gear failure can cause millions of dollars in damage and threaten the life of the crew. As components age, failures associated with metal fatigue or stress-corrosion cracking become more common. We create 3D models of components to allow static analysis, and we assess how usage affects the life of the landing gear, allowing the Air Force to maximize safety while managing maintenance costs.
Monitoring
In addition to laboratory measurements, we install onboard monitoring systems to analyze the stresses that airframes and turbine engines undergo during various flight maneuvers. This helps engineers determine where cracks will occur and how fast they will likely grow. This also helps engineers determine how often inspections are needed. We have extensive experience monitoring how military and commercial aircraft are used to provide data for structural and engine life assessments. These flight recording programs define aircraft maneuver and stress spectra for fatigue analysis and assess the structural stresses associated with various flight maneuvers. They also define temperature and pressure limits that contribute to engine stall conditions. These are already flying on T-38 and A-10 aircraft.
The A-10, which first flew in 1972, is expected to continue in service until at least 2040. Specialized SwRI-developed inspection probes and nondestructive inspection systems include sensors that can inspect through a bushing that does not require removal. In addition, our patented magnetostrictive sensors (MsS®) provide ongoing structural health monitoring on the A-10.
Because the Air Force intends to fly the T-38 supersonic training aircraft until 2034 or longer, we have worked with the Air Force since the 1970s to maintain the plane’s structural integrity. Our systems look for cracks and structural degradation that would endanger the aircraft.
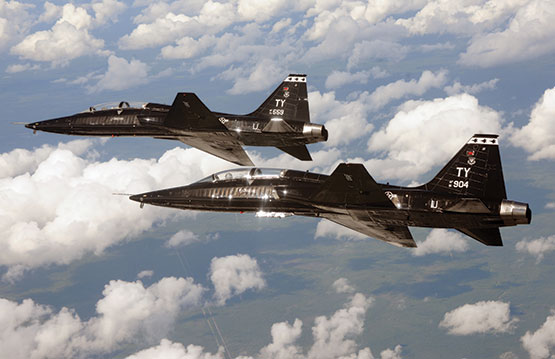
Courtesy of USAF/Master Sgt. J S. Wilcox
To keep the T-38 in service through 2034 or later, SwRI performs usage monitoring, developing inspection methods and schedules for testing at the fleet as well as the component level and conducting analyses to ensure the aircraft structure remains viable.
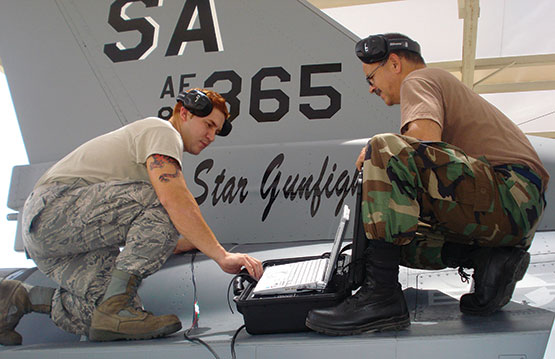
SwRI’s patented magnetostrictive sensors (MsS®) provide ongoing structural health monitoring for military aircraft.
In another project, SwRI conducted flight data testing on the T-38A/B to support a specialized adversary air training program for the F-22 Raptor. Over the course of nearly a decade, seven aircraft were fitted with a flight data recorder and sensors to monitor the critical structural parameters, including airspeed, altitude, vertical acceleration and strain on the horizontal stabilizer torque tube.
Friendly foreign militaries using American aircraft also need to monitor and manage engine maintenance, but legacy applications are difficult to use and do not meet current demands. More than a decade ago, SwRI developed and fielded the Engine Tracking Database System (ETDS) for F110 engines used in the F-15 and F-16 to serve these clients. In addition, SwRI is finalizing a Jet Engine Maintenance Management Application (JEMMA) to support F100 engines that power the F-15 Eagle and F-16 Fighting Falcon. The systems support all existing engine configurations for both the F100 and F110 and can be adapted for new engines without software changes.
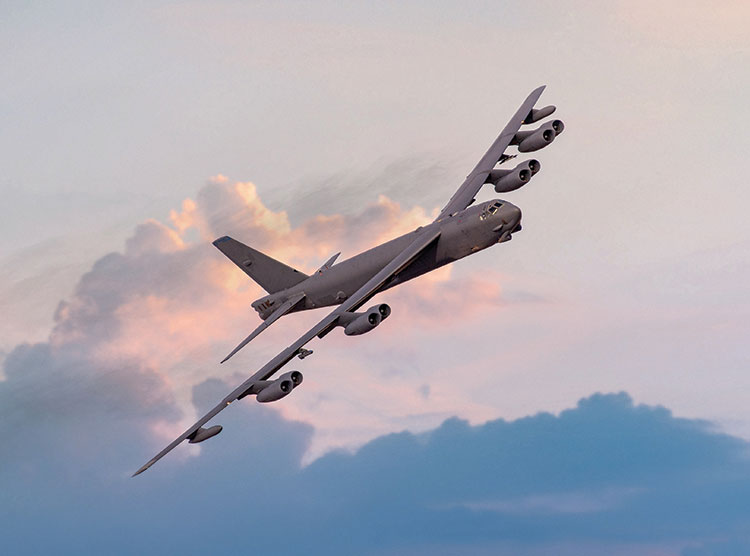
SwRI is adapting a multichannel, audio-visual mission data recording system for the Air Force’s fleet of B-52 bombers. SwRI will ensure the system meets Department of Defense and other regulatory requirements.
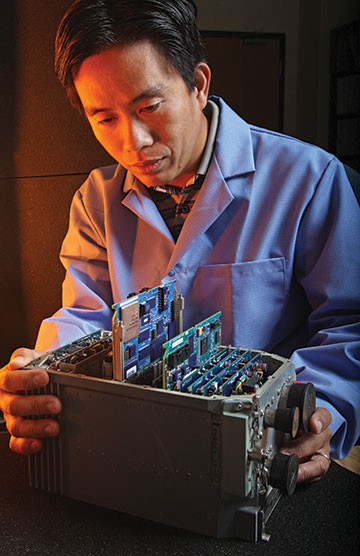
The SwRI-developed Improved Electronic Processing Unit combines engine turbine monitoring and aircraft structural integrity systems into a single, consolidated line-replaceable unit for the entire A-10C fleet.
Both ETDS and JEMMA track maintenance cycles, engine configurations, engine/part installations and removals, maintenance time limits and periodic inspection completion. The systems track engine/part status and document the maintenance history of engines and components. Numerous reporting features alert users to missing or upcoming inspections or when parts approach their life limit. These web-based systems can be fielded in a stand-alone single-base configuration or in a “headquarters” configuration where data from multiple bases are compiled into a single database. ETDS and JEMMA provide flexibility by allowing users to add new part numbers, inspections and life limits. With SwRI’s experience developing JEMMA and ETDS, support for additional engines could be accomplished at a significantly lower cost and shorter schedules than ground-up development.
Modeling
Measurement and monitoring data collected from an aircraft fleet can provide significant inputs to specialized software programs to model fatigue crack growth and fracture in structures and mechanical components. We have developed, and continue to upgrade, software tools to model crack growth that help predict where cracks or other integrity issues might arise and ensure the safe life of the structure. These damage tolerance analysis (DTA) software tools assess the fracture risks of critical equipment. For example, SwRI and NASA’s Johnson Space Center have worked together since 2000 to develop NASGRO®, a DTA tool now used extensively by the space, aircraft, and rotorcraft industries, among others.
A separate effort to develop a probabilistic DTA tool for aircraft engine rotors began at SwRI after a passenger airliner crashed in Sioux City, Iowa, in 1989 following a catastrophic uncontained turbine disk failure in one of its three jet engines. While the captain was able to steer the disabled aircraft to an airport by skillfully alternating power between the two remaining engines, the airplane cartwheeled on landing, resulting in the death of 112 of its 296 passengers and crew.
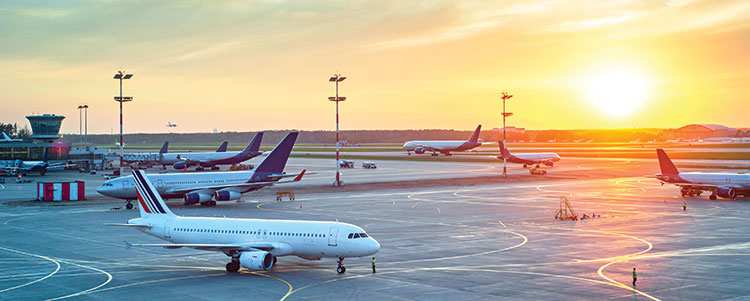
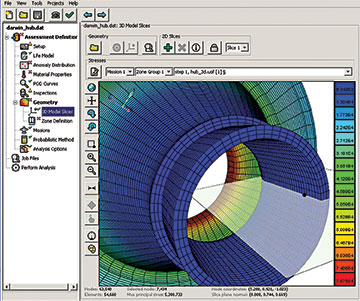
DARWIN helps a user visualize and manipulate 3D component models, identifying the surface location where a crack might initiate. The software tool then slices the model along the plane where the crack is most likely to grow to determine the stresses that will govern its growth.
In response, the Federal Aviation Administration (FAA) sought to improve commercial aircraft engine safety using software to model and manage the risk of fracture in high-energy rotating components. A key outcome of this work was an SwRI engineering team’s development of DARWIN® (Design Assessment of Reliability With INspection), a fracture mechanics and reliability assessment software system that supports damage-tolerant design and analysis of metallic structural components. DARWIN can predict the probability of fracture during the lifetime of each engine, over the entire fleet of engines, based on the probability that an undetected anomaly may occur in the engine rotor during its manufacture.
Aircraft engine manufacturers worldwide use DARWIN to ensure their engine designs are resistant to dangerous cracks. The software helps designers visualize and manipulate a two- or three-dimensional component model, identifying locations where a crack might initiate, slicing the model along the plane where a crack is most likely to grow, and determining the stresses that will govern the crack’s growth rate.

In collaboration with NASA’s Johnson Space Center, SwRI developed NASGRO®, a deterministic data tool for fatigue crack growth and fracture analysis. Our team holds regular NASGRO training for users in the aircraft and space industries.
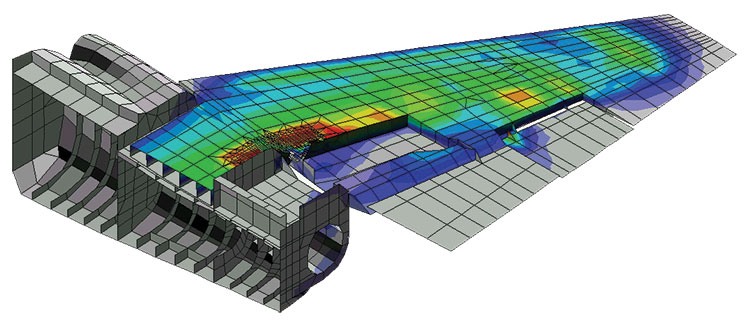
SwRI applied finite model stress analysis of a fighter-trainer aircraft wing to predict stress profiles.
This work has continued to evolve as new incidents occur. For example, in 2016 a disk fracture and resulting engine fire aboard an aircraft at Chicago’s O’Hare International Airport was caused by a material anomaly in a rotor manufactured from a nickel-based alloy. Building on 25 years of continuous funding, the FAA recently funded SwRI to address this new threat through the Probabilistic Integrity and Risk Assessment of Turbine Engines program, which is now in its third phase.
Maintenance
Measuring, monitoring and modeling all are used in maintenance programs to prevent an aircraft from slipping into a state of unknown airworthiness. However, if airworthiness issues lead to a fleet being grounded due to some unknown risk, SwRI engineers then address specific maintenance challenges, creating better ways to test and repair components and avionics systems.
For example, NASA astronauts use the 50-yearold T-38 supersonic trainer for pilot proficiency training. Components of this legacy aircraft must be tested periodically and proven reliable. To this end, SwRI engineers developed a T-38 aircraft-mounted accessory drive test stand to autonomously perform generator and gearbox testing. In 2019, we upgraded the control hardware and software to perform additional automated generator tests. Since that upgrade, NASA has used the test stand to support U.S. Air Force F-5 fighter aircraft as well.
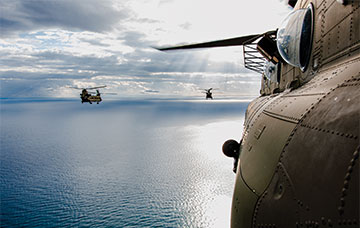
Courtesy of Spc. Mathew Pous
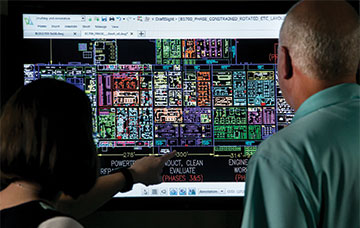
SwRI engineers are designing next-generation flexible manufacturing layouts for efficient workflows for the Army’s helicopter maintenance facilities in Corpus Christi, Texas.
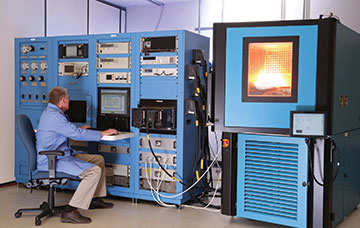
To support a foreign aircraft maintenance depot, SwRI designed and built an automated test system to evaluate an advanced engine control system used on the F-15.
SwRI is working with the Air Force maintenance community to develop a support equipment roadmap (SER) for specific airframes. This process assesses the status of support equipment. It catalogs current deficiencies, unneeded equipment, opportunities for consolidation and current and future requirements, all while assessing the equipment’s ability to support modernization and technology advancements. It also integrates data to generate a funding roadmap to help plan for needed updates or equipment replacements.
The roadmap for the F-15 fighter has completed its data collection phase, while other SERs for the B-1 and B-52 bombers are under development to maintain and modernize equipment at the organizational, intermediate and depot levels. This maintenance system analysis includes plans and procedures that address modernization and sustainment challenges. We also have applied our long experience with the A-10 community to perform studies and provide engineering support, including initiating an A-10 SER a decade ago. Since 2000, SwRI staff also have provided critical onsite engineering support for the A-10 System Program office, troubleshooting problems with field units.
From 2004–2008, we supported flight testing and maintenance activities for the last major avionics upgrade for the A-10. SwRI also helped develop the Digital Fuel Quantity Intermediate Device and Improved Electronic Processor Unit (IEPU) for the plane’s Turbine Engine Monitoring System. The IEPU software is responsible for acquiring signals, detecting engine, aircraft and structural events, and storing related data for later analysis by ground personnel.
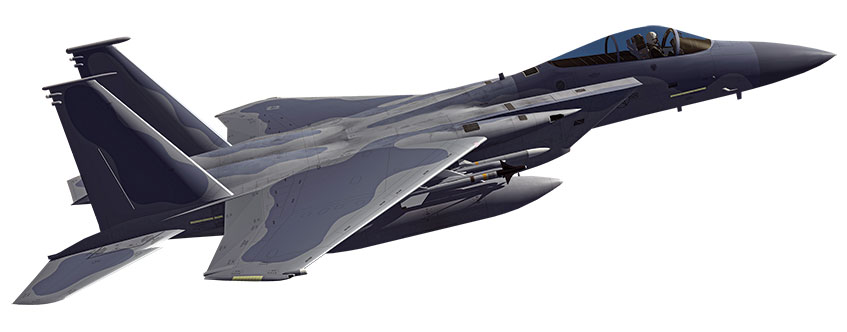
SwRI visited U.S. Air Force bases supporting F-15 Eagle fighters to assess how access to maintenance support equipment affects aircraft availability.
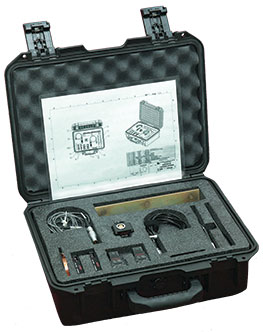
SwRI developed inspection kits for the T-38 aircraft, including steel dorsal longeron and vertical stabilizer tip kits.
SwRI managed a program to replace the primary maintenance and repair facility at the Corpus Christi Army Depot (CCAD) from concept through equipment selection, process flow and construction requirements. The CCAD is the Army’s Center of Excellence for servicing the UH-60 Black Hawk, CH-47 Chinook, AH-64 Apache, OH-58 Kiowa, and the Air Force HH-60 Pave Hawk helicopters. Since 2014, SwRI also has identified key equipment and infrastructure requirements for separate units of a new building to replace an aging and inefficient Maintenance, Repair, and Overhaul (MRO) facility, which will be added sequentially over time.
We have developed a detailed concept of operations, systems and equipment specifications for new work cells at CCAD. These concepts outline material handling, production control, cost, and equipment maintenance management methodologies or approaches. For instance, CCAD performs maintenance on the T55 family of turboshaft engines that power the CH-47 Chinook and MH-47 helicopters. The SwRI team has reverse-engineered and redesigned an engine test cell control console to replace unreliable and unsupportable technology, documenting, integrating and evaluating the newly designed console.
Modernization
As air fleets age, their avionics can become increasingly difficult to support and maintain, and their capabilities often do not meet today’s demands. However, replacing and modernizing systems and components can be challenging, and the military must rely increasingly on commercial off-the-shelf (COTS) technologies for its avionics hardware and software.
Although COTS items are generally less expensive than comparable items designed to military specifications, the COTS technology-refresh cycle is typically 18 months or less. This exacerbates the obsolescence problem for aircraft whose lifetimes are measured in decades. The short refresh cycle is driven mostly by the tremendous advances in computer systems, which comprise an increasing percentage of avionics systems.
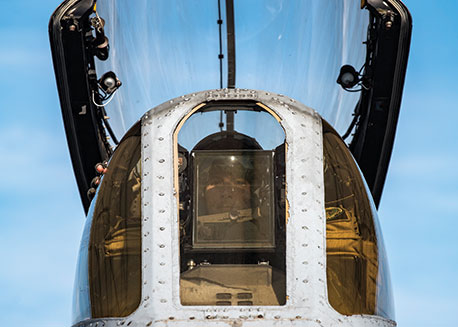
Courtesy of USAF/Airman 1st Class Eugene Oliver
This AF pilot is looking through the A-10’s head-up display (HUD), which digitally provides important information to pilots without requiring them to look away from the flight path. SwRI is upgrading the Flight and Fire Control Computer processor and display electronics to address critical aircraft supportability issues.
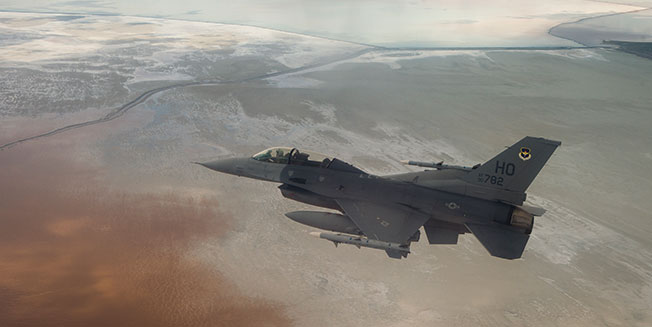
Courtesy of Staff Sgt. Andrew Lee
In 2019, SwRI developed a new Sensor Integration Unit (SIU) subsystem for the F-16 Fighting Falcon to consolidate, modernize and replace legacy systems. The new technology integrates threat and target sensing while maximizing the utilization of the various RF subsystems and embedding avionics cybersecurity, a recent mandate for all new avionics subsystems.
To address military aircraft system sustainment, obsolescence and modernization, SwRI has conducted numerous Form, Fit, Function and Interface (F3I) programs to update or upgrade aircraft components or avionics. An updated item is F3I-compatible when it can be inserted into an aircraft without negatively impacting legacy components or overall operations.
DETAIL
Targeting pods are tools used by ground-attack aircraft to identify targets and direct precision-guided munitions.
In 2021, SwRI began redesigning a system on the B-1B Lancer, a long-range supersonic bomber that the Air Force introduced in the 1980s, to allow it to remain in service until 2040. We are redesigning the Lancer’s Fuel/Center of Gravity Management System (F/CGMS), which tracks fuel data and usage, controls fuel transfer to the aircraft’s four turbine engines and calculates corrections to the bomber’s center of gravity as fuel is depleted. The redesigned B-1B fuel-balance system can be inserted into the aircraft to provide vital in-flight data and support the aircraft’s next phase of service.
Other ongoing support for the B-1 fleet involves material and structural joint testing and airframe analysis of fatigue-critical locations, including Taper-Lok™ fasteners and coldworked holes. These life-enhancement technologies are designed to strengthen metallic components and extend fatigue life but can complicate structural analysis. SwRI is helping Boeing and the Air Force understand life improvement gained using these technologies to set appropriate maintenance intervals.
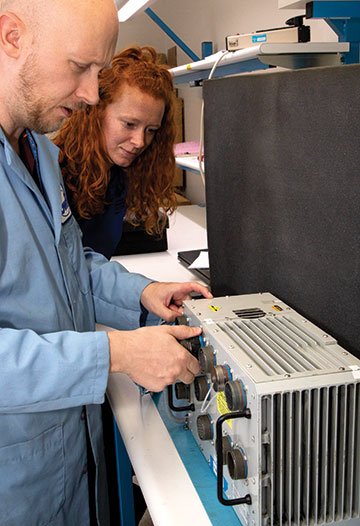
Engineers completed lab and flight test investigations to determine new baseline vibration and temperature environments and redesign the A-10C Thunderbolt II’s central interface control unit.
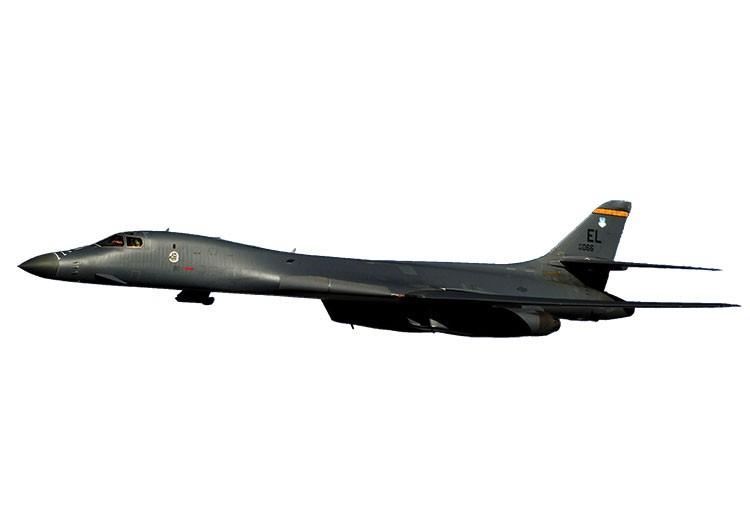
Courtesy of USAF Master Sgt. William Greer
SwRI is redesigning various B-1 system components — including the intermediate device chassis, power supply and assembly of multiple interface module circuit cards — which must work with the new designs while maintaining compatibility with the legacy design. The redesign introduces other new challenges for SwRI engineers, as it is the first time the team will incorporate radiation hardening into flight system designs.
After two decades of maintenance support for the A-10, SwRI was well-positioned to help with the design and implementation of upgrades. For example, we helped develop a modern Digital Stores Management System that turned unguided, free-falling bombs into precision-guided munitions. An upgraded Integrated Flight and Fire Control Computer improves computer-aided capabilities and adds symbols to the pilot’s head-up display to support targeting pods, data links and smart weapons integration.
To address advances in adversarial targeting systems, signals intelligence (SIGINT) specialists at SwRI are helping U.S. and allied militaries gather communications intelligence, fueling capabilities in electronic warfare (EW) that use electromagnetic techniques to thwart hostile operations. SwRI supports EW techniques and technology to control the electromagnetic spectrum and deny advantages to an opponent, while ensuring friendly dominance of the spectrum. For example, SwRI is developing modular Ravager EW technology designed to maximize operational effectiveness and flexibility in response to emerging threats, while minimizing future supplier and parts shortages. We are integrating this advanced technology into legacy military EW systems, addressing size constraints and operational profiles of existing and future systems. SwRI engineers are currently developing and integrating Ravager proof-of-concept hardware and software into an existing military system.
Questions about this story or Aerospace & Aircraft? Contact Tim Fey at +1 210 522 3253.
ABOUT THE AUTHORS
From left, Edwin Aulick, a manager in the Defense and Intelligence Solutions Division, oversees hardware, software and firmware development efforts for embedded aerospace avionics applications. Roger Lopez, a manager in the Applied Physics Division, specializes in hardware and software systems ranging from commercial test equipment to military avionics. Tim Fey, director of the Structural Engineering Department in SwRI’s Mechanical Engineering Division, oversees research supporting the aerospace, telecommunications, nuclear, marine and oil and gas industries, as well as U.S. and allied military programs.
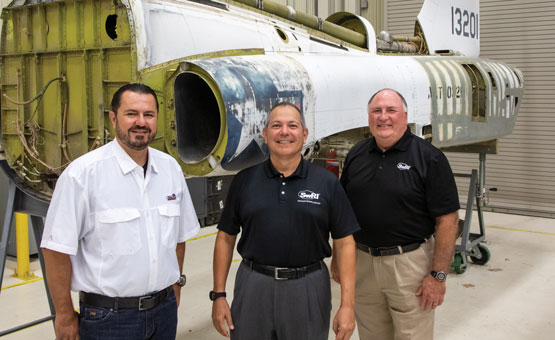