BACKGROUND
The oil and gas and petrochemical industries have a need for thick diamond-like carbon (DLC) coatings on the interior surface of long pipes to increase corrosion and erosion resistance. Using a plasma immersion ion deposition (PIID) process, SwRI has demonstrated that thick (>10 µm) DLC coatings can be deposited on the outer surfaces of components. The coatings have shown excellent corrosion resistance in salt water and CO2 environments, which are commonly seen in O&G fields.
SwRI also has developed a PIID-based coating process by which a thin functional (hydrophobic) coating can be deposited on the interior surface of long pipes up to 80 ft. long to prevent hydrate from clogging the pipes. To date, however, SwRI has been unable to deposit thick DLC coatings (5-10 µm) for erosion/corrosion protection in long pipes. Therefore, the objective of the project is to develop a coating technology by which thick, corrosion resistant DLC coatings can be deposited on the interior surface of long pipes (30-40 ft.).
APPROACH
Initial coating development is carried out on 7 feet long pipes (4 inch diameter) to optimize key deposition parameters and power supply configurations. Stainless steel coupon samples are placed inside the pipe for characterization and process optimization purposes.
The efforts are focused on developing a stable PIID process for obtaining high quality thick DLC coatings in long pipes. The corrosion resistance of the DLC coatings on coupon samples will be evaluated using electrochemical impedance spectroscopy (EIS) tests, salt spray test, and scaling resistance test. After successfully depositing high quality thick DLC coating (5-10 µm) on coupon samples in 7 ft. long pipes, the coating process will be transferred and demonstrated on large aspect ratio pipes (30 ft. long, 4 inch diameter).
ACCOMPLISHMENTS
Different power technology configurations (AC, pulsed dc, high power impulse pulsed dc) for the pipe and electrode were optimized to improve the uniformity and density of the plasma generated in long pipes for DLC depositions. The structure and properties of DLC coatings have been studied systematically by tuning key processing parameters and using different power technology configurations. To date, the as-deposited DLC coatings exhibit super dense structure and good adhesion.
Figure 1 presents the cross-sectional and top view scanning electron microscopies (SEM) of a typical thick DLC coating deposited on the interior surface of a 7 ft. long pipe. It is evident that the coating shows very smooth and dense surface morphology.
The hardness of the coatings was measured using nanoindentation.
The tribological properties of the DLC coatings were evaluated using ball-on-disk (dry) wear test. It is found that the typical DLC coating deposited on the interior surface of pipes exhibits high hardness of 15-20 GPa and COFs of 0.1-0.15 in dry sliding condition. The corrosion resistance of the DLC coatings are currently under investigation. The optimized coating technology is going to be transferred and demonstrated on large aspect ratio pipes in the near future.
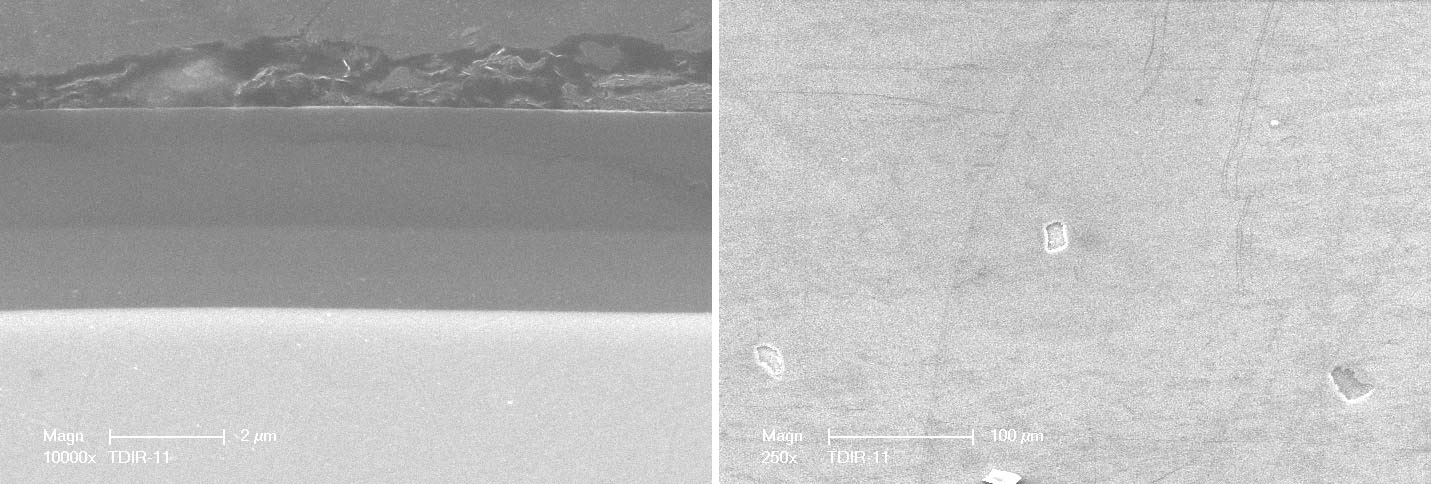
Figure 1: (a) Cross-sectional and (b) top view SEM micrographs of a thick DLC coating deposited on the interior surface of a 7 feet long stainless steel pipe (diameter of 4 inches).