BACKGROUND

An internally cooled radial turbine will be needed within the next five years to keep up with the trend in the power generation industry to increase both the efficiency and the modularity of power production. Specifically, a cooled radial turbine will be needed for supercritical CO2 (sCO2) power cycles, power cycles utilizing oxy-combustion, and conventional generation systems. Internally cooled radial turbines have been successfully designed, manufactured, and tested in the past. However, conventional manufacturing methods are difficult to apply to a radial impeller in a cost-effective manner. The conventional manufacturing method is an investment cast process using a ceramic core to create internal passages. This approach has been developed for axial gas turbines and is a low-risk manufacturing approach for axial blades. For radial impellers, however, the entire impeller blades and the hub are typically manufactured from a single piece of material. Therefore, if one blade casting has an error, the entire part must be thrown away. By including ceramic cores in the casting process of an entire radial impeller, there is a risk of core misalignment or wall breakout for any of the cores in the casting.
To overcome the complexity and reduce production risk, additive manufacturing can be used to build internally cooled radial turbines. Additive manufacturing is a growing area and gaining operational experience is required to confidently build complex parts, such as a radial impeller with small, internal passages. In this project, additive manufacturing is being used to avoid the challenges of conventionally manufacturing radial gas turbines with internal cooling.
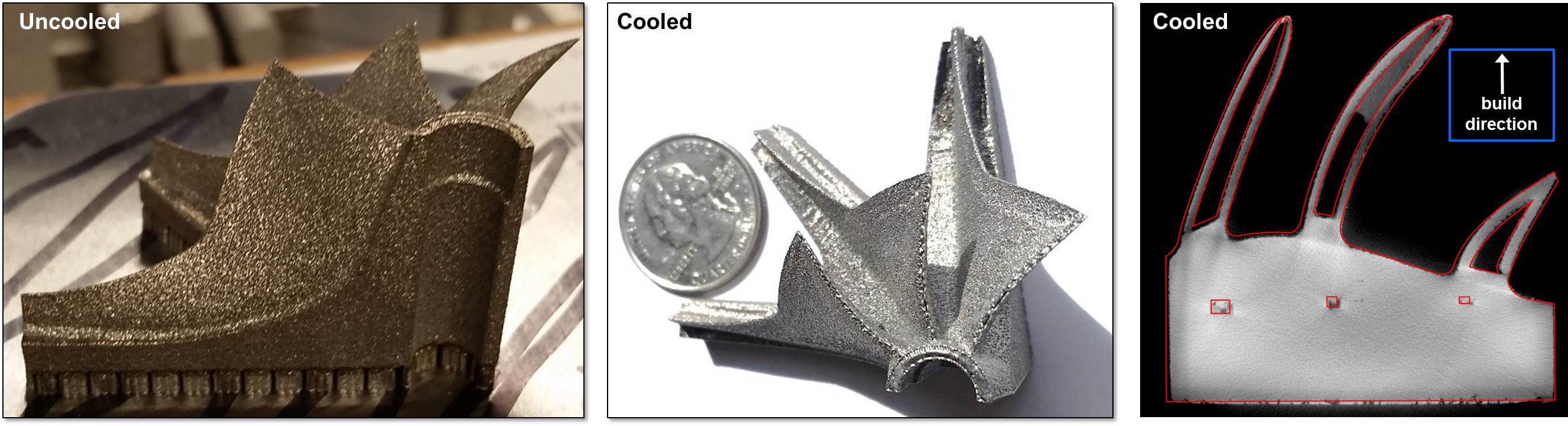
Figure 2: Both uncooled (left) and cooled (middle) impeller sectors have been successfully manufactured to show the capability in resolving blade thickness and orientation angles as well as hollow blade features (right, CT scan).
APPROACH
An internally cooled impeller will replace a solid impeller designed for a 12.5 kW radial gas turbine generator (Figure 1). The impeller has a diameter of 90 mm (3.3”) and rotates at 118,000 rpm. Cooling channels are used inside the impeller to reduce the maximum metal by 230° C. Prior to manufacturing the cooled impeller, multiple printing trials are needed to better understand the additive manufacturing build process for the impeller as well as characterize the material properties.
ACCOMPLISHMENTS

The preliminary cooling design for the impeller has been completed and a sector of the impeller has been manufactured. For comparison, a solid, uncooled impeller was also manufactured. For both parts, the manufacturing resolved the small blade thicknesses and orientations as well as the internal passages (Figure 2). Predictions of part distortion have agreed well with the actual part distortion, as measured using CT scanning and using a coordinate measuring machine. The next steps in the project are to complete the next build iteration (Figure 3), conduct material testing, and conduct air flow testing of the internal passages.