Background
Predicting the material properties, strength, and durability of components resulting from AM processes is a complex problem. Layer-by-layer deposition of material during an AM process produces potentially severe residual stresses that distort components, introduce non-homogeneous microstructures, and alter material properties from the wrought condition. Potentially, engineers may tailor these (and other) quantities in the AM process based on performance requirements using integrated computational materials engineering (ICME) approaches. However, before tailoring these quantities towards a performance goal, we must first predict them accurately, and this requires a comprehensive simulation framework to model the AM process.
Aberration-correction is achieved by interfering two recording lasers on a photoresist, creating grooves that can be configured by changing the input angles and distances from the grating to the lasers. The grooves created by holography can have variable spacing that are curved, providing additional optical power in a controlled fashion. By optimizing the location of the lasers in conjunction with the optical performance of the spectrograph, the capability of a given spectrograph may be dramatically improved. However, these techniques have the limitations of quantized and finite laser recording wavelengths. The created grooves have only a few free parameters and, therefore, the grooves are functionally related everywhere on the grating.
Approach
This project presents a comprehensive analysis framework to predict thermal histories, residual stress, distortion, microstructure, and material properties in components built using the additive manufacturing (AM) process of powder bed fusion driven by selective laser melting. SwRI developed this analysis framework as a part of the internal research MAKERS program. The hierarchical computational framework developed during this work employs several models with varying computational complexity to achieve computationally tractable results.
This framework first initiates a thermal analysis of the AM process, and the thermal analysis supports detailed laser scan strategies, activation of simulated layers, and material phase changes. This framework employs relatively straightforward thermal simulations using a one-way structured grid of finite elements oriented in the build direction. As a layer of powder is deposited, the associated elements activate and contribute to thermal processes — primarily by conducting heat from node to node. The distributed surface flux moves from location-to-location based on a user-defined laser scan path. Heat generated from the laser conducts heat throughout the material during the AM process. These analyses transmit thermal energy along the surface by gas-to-solid heat convection and thermal radiation. The build plate represents a heat sink. Material properties may (or may not) exhibit a one-way phase change from powder to liquid and then between liquid and solid based on the temperature. Figure 1 shows a demonstration of the thermal modeling capability.
The resulting thermal histories drive structural-scale predictions of residual stresses and residual distortions. This framework employs continuum scale simulations using the same one-way structured grid of finite elements. Here, previously-computed thermal histories drive analyses to compute residual stress development. All elements have a load carrying capacity that reflects its thermo-mechanical response in the elastic-plastic regimes. These elements expand/contract as the temperature increases/decreases and, if the element is constrained, thermal expansion triggers residual stress build-up. The build plate constrains elements immediately adjacent to it.
The thermal histories can also drive predictions of microstructural quantities and mechanical properties. This framework employs hierarchical, physics-based models, e.g., the three-parameter phenomenological model for average grain size by Van Bohemen. Results from this framework are driven by the simulated time-temperature response of a mesoscale model of the thermal history. Calibrated parameters align predicted microstructural features with analogous measured features in the as-built configuration and in the post-HIP condition. This framework supports grain size predictions and volume fraction predictions of α and β phases using CALPHAD methods. Finally, this framework employs an informed machine learning approach to calculate stress-strain curves of AM Ti-6Al-4V based on open literature mechanical property data.
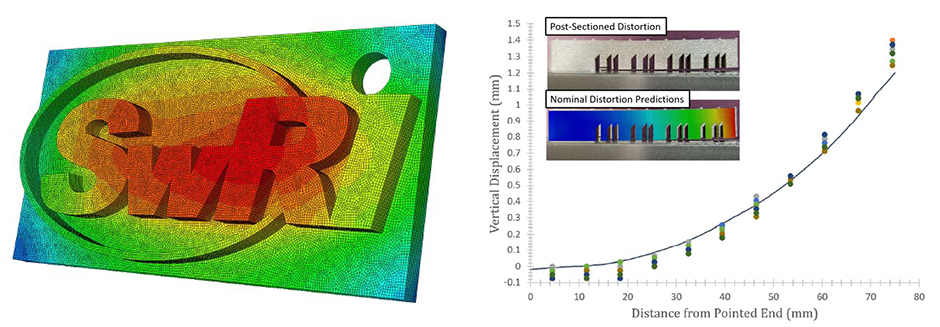
Figure 1: (Left) Demonstration exercises of the thermal process model. Figure 2: (Right) Post-sectioned distortion for the NIST test specimens vs. nominal SwRI prediction.
Accomplishments
- Activate simulated layers of elements to approximate layer-by-layer deposition.
- Define a surface flux consistent with the laser scan path.
- Change material phases between powder, liquid, and solid.
- Predict thermal histories at mesoscales and structural scales.
- Predict residual stress accumulated during AM build process.
- Predict residual distortion after cutting part from build plate.
- Predict microstructural quantities of interest, including average grain size.
- Propagate microstructural quantities of interest to predict material properties.
Accomplishments during this project include an AM process framework with capabilities including:
This project includes efforts to validate the computational modeling framework using SwRI’s Renishaw AM250 machine. Measurements from the NIST-designed test coupons built at SwRI validate predicted residual distortion and microstructure from the computational framework. Twelve of these geometries were built using SwRI's Renishaw AM250 machine. Residual distortion measurements were conducted on several specimens. Metallurgical investigations were conducted on one test specimen that was sectioned and examined. SwRI exercised the AM process framework to predict residual distortion (a proxy of residual stress) and microstructural features of the build. Residual distortion predictions were typically within the scatter of experimental measurements as shown in Figure 2. Grain size predictions were within the range of measurements as well. Additional efforts apply this framework to a redesigned aerospace component. These efforts demonstrate that the computational framework provides a reasonable prediction of measured distortion. Sensitivity studies of the mesoscale modeling capabilities suggest that hatch spacing is the key processing parameter to control β grain size as shown in Figure 3.
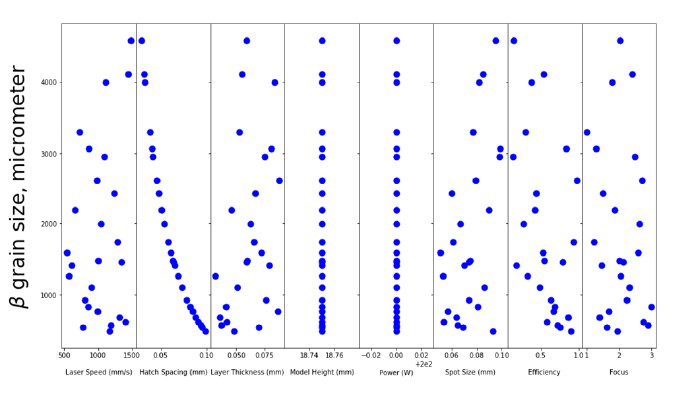
Figure 3: Sensitivity of β grain size to AM process parameters for Ti-6Al-4V.