Background
SwRI has been at the forefront of the surge in robotics with the development of advanced path planning software through the ROS-Industrial Consortium. In a modern system, advanced perception detects and generates a process path within the work volume. Next a robot trajectory is generated to move the tool through the desired process path. Finally, the motion is executed on the robot. However, once the robot trajectory is generated, the ability to make modifications to that trajectory to account for movement in the process path or introduction of obstacles is limited. This research worked to bridge the gap from on-demand path planning, that can take up to several seconds, to real-time path planning that must operate at much higher frequencies (defined here as at least 50Hz).
Approach
The proposed approach was to use a SwRI-maintained optimization-based path planner, known as TrajOpt, and improve it leveraging a GPU to run at "real-time" speeds (i.e. fast enough for real-time capability) when taking single steps of the optimization. The teams proposed approach was to update paths to changing environmental conditions during execution. Importantly, these improvements were carried out in simulation only, with this research serving as a feasibility study for future implementation on robotics hardware.
Accomplishments
The project proposal put forth two benchmark applications. Both applications used a 6 degree-of-freedom (DOF) robot suspended underneath a 2 DOF gantry. One application then sought to use real-time trajectory updating to follow a toolpath that was drifting by some velocity. The other application sought to avoid dynamic obstacles in the environment. Success for this project was defined as the ability to update a robot trajectory at a frequency of at least 50 Hz in both applications, which was easily achieved. Figure 1 shows the system planning around a static collision obstacle while tracking a toolpath moving in a sinusoidal motion with an amplitude of 1 meter and a period of 5 seconds, resulting in a max velocity of approximately 800 mm/s. Figure 2 shows the second benchmark wherein the system is planning a fixed toolpath while avoiding a dynamic obstacle where the dark red cylinder represents a human moving around the volume and the light red cylinders represent a human-free zone protected by safety LIDAR. A single dynamic obstacle was added for simplicity. The system supports an arbitrary number of obstacles.
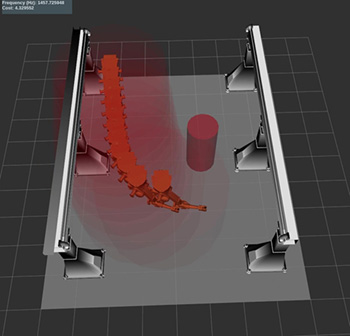
Figure 1: System (gantry not visible but included in the optimization) tracking a toolpath moving in a sinusoidal pattern while avoiding a static obstacle.
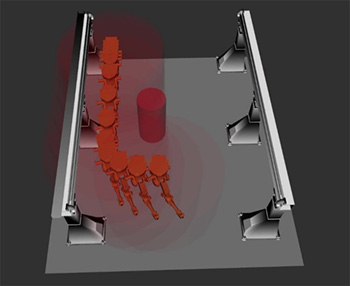
Figure 2: System (gantry not visible but included in the optimization) planning a trajectory around a dynamic collision obstacle moving in a sinusoidal pattern.