Background
The automotive industry is investing billions of dollars in electrification, and SwRI is working to extend its expertise in precision efficiency testing of internal-combustion engines to electric machines. Efficiency testing can be conducted using a vehicle mounted on a chassis dynamometer, but more precise results are obtainable by removing the drive unit (motor, gear reduction, and differential in a single housing) and operating it on a motor dynamometer. Unfortunately, without inputs from the rest of the vehicle, the stock inverter will not run the drive unit. Additionally, we hypothesize that it is possible to improve the efficiency of a motor by optimizing the inverter’s switching frequency. This project thus has two goals:
Demonstrate the ability to operate an ex-vehicle drive unit on a dynamometer by duplicating the stock control strategy on a programmable (usually called “open”) inverter.
Explore non-stock switching frequencies to improve the motor’s efficiency.
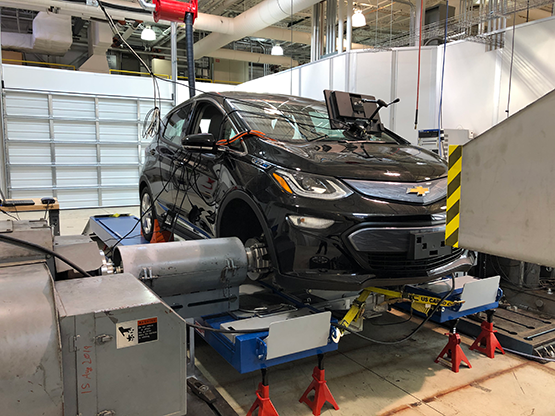
Figure 1: The Chevrolet Bolt mounted on the hub dynamometer, which measures speed and torque directly at the wheel hubs.
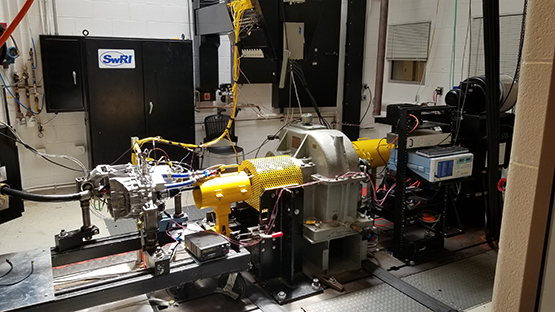
Figure 2: The Tesla Model 3 drive unit mounted to a gearbox and dynamometer in a test cell configured for electric machines.
Approach
This project consisted of three phases:
Benchmark the efficiency of an electric vehicle. Reverse-engineer the stock control strategy.
Characterize the efficiency of an ex-vehicle drive unit operated by an open inverter that has been programmed with the stock control strategy.
Measure the effect on inverter, drive-unit, and system efficiency of varying switching frequencies.
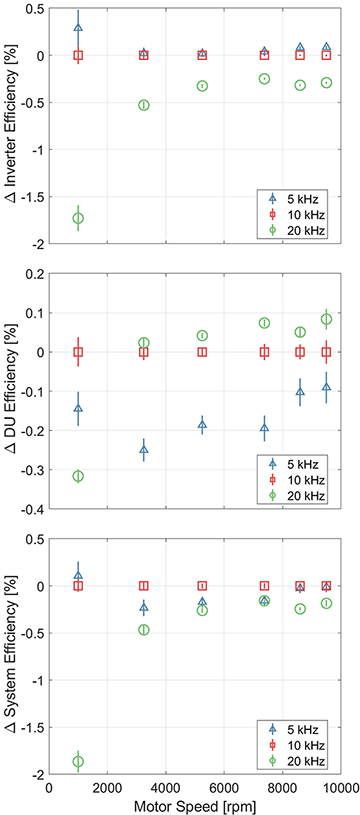
Figure 3: As switching frequency increases, inverter efficiency decreases, while drive-unit efficiency increases. A switching frequency of 10 kHz is the optimal for system efficiency.
Accomplishments
We completed Phase 1 using a Chevrolet Bolt mounted on a hub dynamometer, which measures torque at the wheel hubs, without tire slip, as shown in Figure 1. The data obtained included the inverter’s pulse-width-modulation (PWM) strategy, the switching frequency, the electrical efficiency of the inverter, the electromechanical efficiency of the drive unit, and numerous controller-are network (CAN) signals. The Bolt drive unit was reallocated to an urgent customer project, so we completed Phases 2 and 3 using a Tesla Model 3 drive unit, as shown in Figure 2. (The Model 3 and Bolt both use permanent-magnet synchronous motors, so their control strategies are very similar.) In Phase 2, we demonstrated repeatable control of the Model 3 drive unit over much of the stock speed/torque envelope. In Phase 3, we studied how varying the inverter’s switching frequency affected the efficiency of the inverter, drive unit, and complete system (inverter and drive unit together). In Figure 3, the change in efficiency with respect to that obtained at the stock switching frequency (10 kHz) is plotted against motor speed for three switching frequencies. Increasing switching frequency reduces inverter efficiency but increases drive-unit efficiency, as we expected. The data also shows that additional efficiency could be gained by implementing a dynamic switching frequency, in which the switching frequency would change in real time with motor speed.