Background
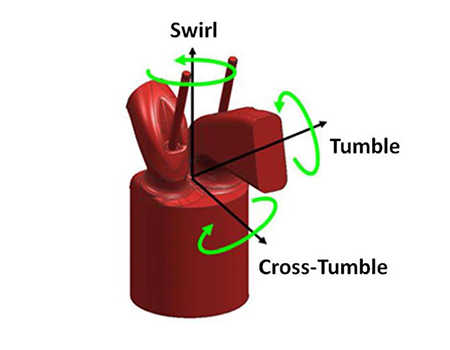
Figure 1: Bulk flow components generated in the intake process.
Natural gas provides a clean, low-cost energy source in many parts of the world. It is of particular attraction in medium and heavy-duty trucking applications where the load factors and daily mileage accumulation preclude battery-electric vehicles. Current production natural gas engines have a significant efficiency disadvantage but benefit from low carbon-dioxide emissions and the lower cost three-way catalysis aftertreatment as compared to diesel aftertreatment systems. To introduce alternative fuel technologies like natural gas to the market, it must offer environmental benefits and compete with the conventional fuel technologies such as gasoline and diesel engines based on investment and operating cost.
Sales volumes of natural gas engines have traditionally been much lower than that of their diesel counterparts and have not justified the design cost and manufacturing investment needed for fully optimized custom designs. The challenge faced by engine companies desiring to develop low-cost natural gas derivatives of a diesel engine is that the cylinder head has been designed for swirling flow instead of tumble flow. These two bulk flow parameters are defined as indicated in Figure 1.
In a diesel engine the valves are arranged in a far-square pattern where the flow through the intake port arrives at one valve first, and then the other as depicted at left in Figure 2. The far-square design allows the air to be directed such that a swirling flow is created as it enters the cylinder. This flow field is retained throughout the compression process and serves to “stretch” the injected fuel sprays, enhancing contact area between the air and fuel, and promoting the diffusion flame of the diesel engine.
In spark-ignition engines the preferred approach is to arrange the valves in a near-square pattern, where the intake flow arrives at both valves simultaneously. This is shown at right in Figure 2. Little or no swirl is generated, but instead the intake flow passes through the valves toward the opposite wall of the chamber. The flow then turns downward toward the piston in what is termed tumble flow. Unlike swirl the bulk tumble flow breaks up as it encounters the upward piston movement during compression, and a simple flat piston can be used. The break-up of the bulk flow field results in fine scale turbulence at the time the combustion is initiated. This turbulence significantly enhances the flame speed. Higher flame speed enables the engine to be operated with higher exhaust gas recirculation (EGR) or at a higher compression ratio at the same knock intensity, thus improving engine efficiency. The turbulence is computationally quantified as turbulent kinetic energy (TKE) and is referred to as such throughout the report.
The retrofit designs replace the fuel injector with a spark plug but do not change the intake flow field. Substantial cylinder head modifications would be necessary to implement the near-square valve arrangement which results in cascading design and manufacturing changes; the valve positions and planes of actuation change, resulting in the entire valve drive system needing to be redesigned. This makes the cost of a well-performing modification prohibitive for most manufacturers, even though natural gas engine sales volumes are increasing, and no such designs have been implemented to date.
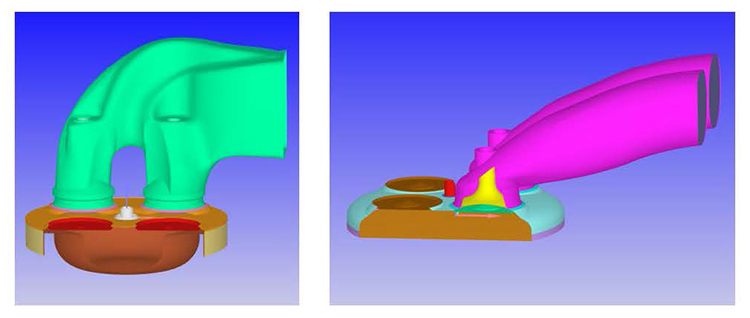
Figure 2: Far-square diesel (left) and near-square spark-ignition (right) intake ports.
Approach
The objective of this research was to seek methods of achieving combinations of tumble and cross-tumble that would generate high turbulence (TKE) and increased energy release rate while using a far-square port configuration. Success in identifying feasible designs will have two important results:
- The distinctive design features that would achieve high TKE with far-square port geometry can be readily defined and patented.
- The ability to achieve high TKE with only a cylinder head modification while retaining the diesel engine’s valvetrain and cam drive system will be attractive to any medium- and heavy-duty engine manufacturers desiring to add natural gas-fueled engines to their portfolio.
The approach taken in this project was to generate various design concepts and evaluate them computationally using the same engine geometry and operating conditions. The evaluation criteria began with tumble and cross-tumble flow generation, and then considered conversion to TKE, and ultimately the impact on combustion energy release rate. Existing computational fluid dynamics and combustion models included both the far-square diesel ports and a conceptual near-square design as shown in Figure 2.
Accomplishments
A wide variety of design iterations was evaluated, with results shown relative to the baseline near-square and far-square ports. Results for several designs are plotted as turbulent kinetic energy versus crank angle in Figure 3. At first look, while each of the concepts showed improvement (increased TKE) as compared to the far-square swirl port, none of them approached the TKE of the near-square port. However, these plots show the resulting TKE only through the intake and compression processes. The impact on combustion and resulting engine efficiency is determined by TKE during combustion. As noted in the expanded diagram on the right in Figure 3 several design concepts did not show the rapid TKE decay of the near-square baseline. Further analysis including combustion was conducted for two of the most promising cases. It was found that early in the combustion process these designs became equivalent to the near-square design. Compared to the baseline swirl port combustion duration was shortened by approximately four degrees crank angle, whereas the near-square port had a five-degree shortening. At least eighty percent of the improvement achievable with a near-square design was achieved with the much simpler to implement far-square tumble port identified in this project.
Patent protection is currently being sought. A marketing presentation is being developed to share with potential clients once the intellectual property resulting from this research has been secured.
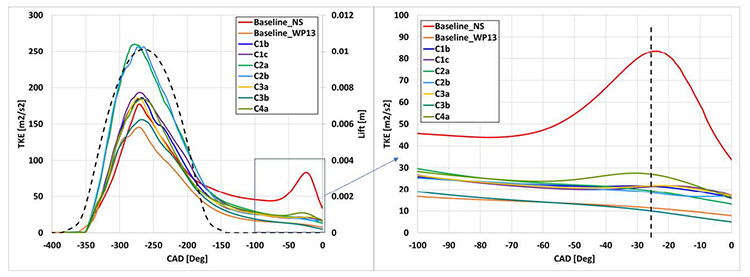
Figure 3: Comparison of TKE versus crank angle between the various concepts.