Background
Propellant management devices (PMDs) are often used within the fuel and oxidizer tanks of flight vehicles to prevent or delay vapor ingestion into the propulsion system. In space, when the location of gas and liquid within a tank are no longer dictated by gravitational forces, there is a risk of ingesting the gaseous phase into the propulsion system and rendering the system inoperable. PMDs are effective because they rely on surface tension to ensure that the liquid propellant is always available to the propulsion system.
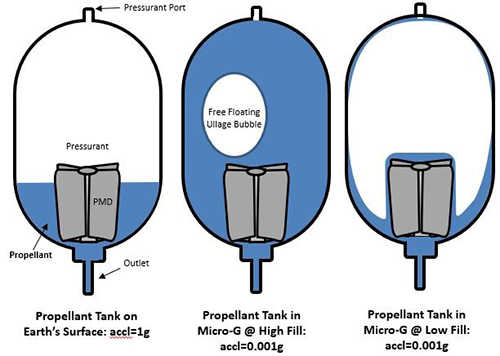
Figure 1: Propellant Tank Example and Scenarios
The design of PMDs relies almost exclusively on analysis with experimental testing being limited or unfeasible. If viable, a common experimental form of testing is drop tower testing which takes a scaled model of the tank and drops it from great heights to produce just a few seconds of micro-gravity behavior. Because of the brief window and scaling required, drop tower testing is commonly used only to confirm CFD static configurations; however, there are risks in the design of PMD’s that warrant looking at dynamic performance. This project utilizes the concept of neutral buoyancy, which is the balancing of gravity and buoyancy forces using equally dense immiscible fluids, to reproduce transient micro-gravity effects on fluid behavior in a ground-based laboratory. The appeal of using a neutral buoyancy approach is that it requires no scaling, can hold a micro-g configuration indefinitely, and can be tested for dynamic situations.
Approach
A plan was devised to create a novel neutral buoyancy PMD test bench. The first task was to select safe, immiscible fluids that can accurately replicate the fluid properties of liquid oxygen in the neutral buoyancy context. Liquid oxygen is a high-performance oxidizer that is critical to future exploration architectures yet have no PMD heritage, making it of particular interest. The second task was to design a representative tank and PMD to be used as the first test case for the new neutral buoyancy test bench. The final task was to construct the neutral buoyancy test stand and simulate dynamic events at the PMD, such as tank expulsion under non-axial micro-gravity accelerations. As an intermediary step between testing a full-scale tank and PMD, a subscale component-level dynamic test will be performed looking at steady state flow through a wedge. Experimental data exists for validation, and additional steady-state vane flow was to be analyzed within standard micro-gravity fluid analysis software, Surface Evolver. This modeling accomplishment is novel itself, provided that Surface Evolver is an exclusively static-based solver and new methods will be applied to extend it to non-static conditions. Overall, a successful project will yield a valuable capability for observing micro-gravity effects on fluids while extending the neutral buoyancy technique to address unexplored flow regimes. Improved testing capabilities and design methodologies will be demonstrated, providing valuable improvements to the market which offer the ability to create improved designs, with less risk, and shortened timelines.
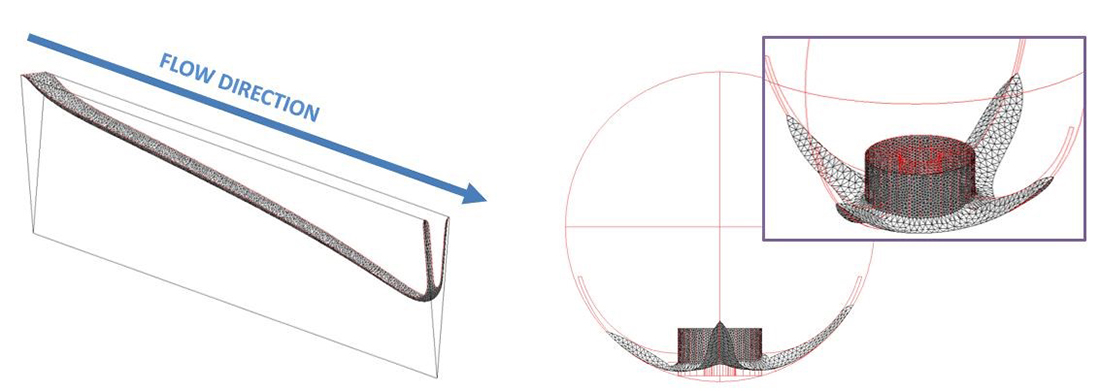
Figure 2: Surface evolver simulations for test apparatuses. (left) Steady State flow through a 5-degree wedge. (right) Static surface evolver simulation at 100 micro-g lateral acceleration at a tank fill level of 2%.
Accomplishments
The project thus far has yielded four solvent mixtures capable of simulating liquid oxygen fluid properties in a micro-g environment. The selected fluid choice is capable of density matching to a level that will produce simulated accelerations of up to 170 micro-g. In addition, a polycarbonate test tank, PMD, and isolated wedge test apparatus have been designed and manufactured and await assembly of the full system. The majority of the major fluid handling and test assembly components have been designed, ordered, and received. New methods have been successfully applied to model transient behavior in Surface Modeler and predictions compare well with experimental data. The project has received a six-month extension to allow time for final assembly and integration, commissioning, and testing of both the isolated wedge and the full-scale test tank with the PMD installed.
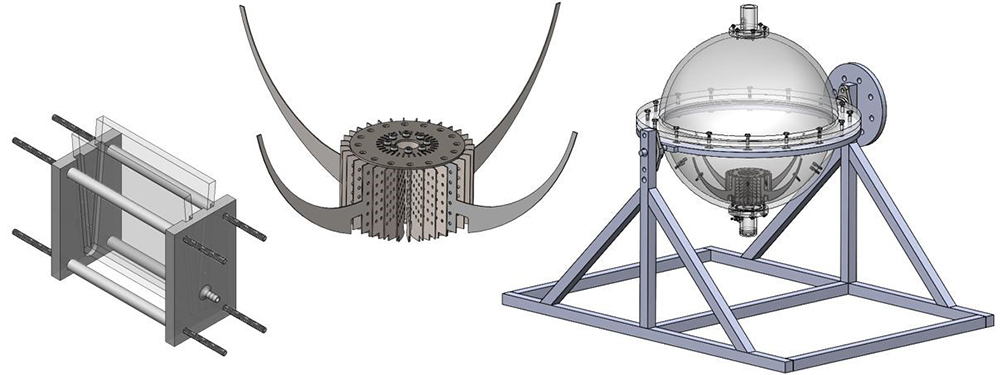
Figure 3: Designed components. (Left to Right) Wedge test apparatus, sponge and vane PMD design, neutral buoyancy test bench.
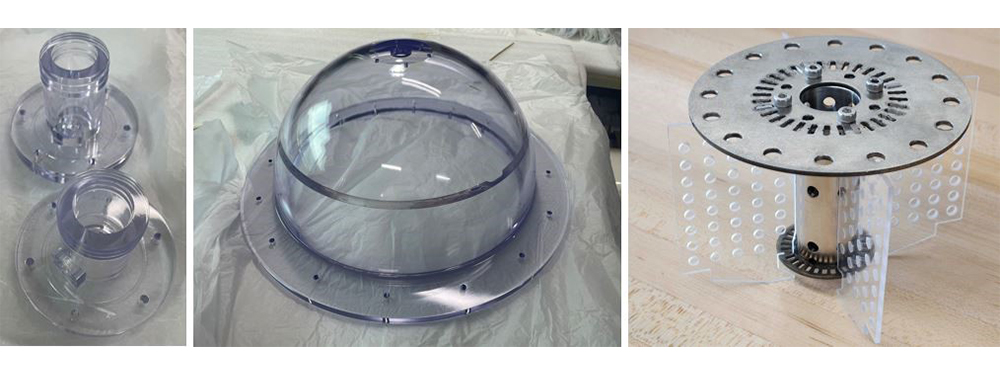
Figure 4: Manufactured components. (Left to right) Outlet connections, Tank half, PMD sample panels installed.