Background
Vibration analysis is commonly used for health monitoring and troubleshooting issues with machinery such as pumps, compressors, gas turbines and electric motor drives. Recorded measurements from vibration sensors are normally studied using Fast Fourier Transform (FFT) based frequency analysis, however FFTs are not well suited to analysis of short term transient waveforms. Time-frequency based techniques have more promise, but these analysis techniques have not been widely applied to troubleshooting machinery vibration problems.
Approach
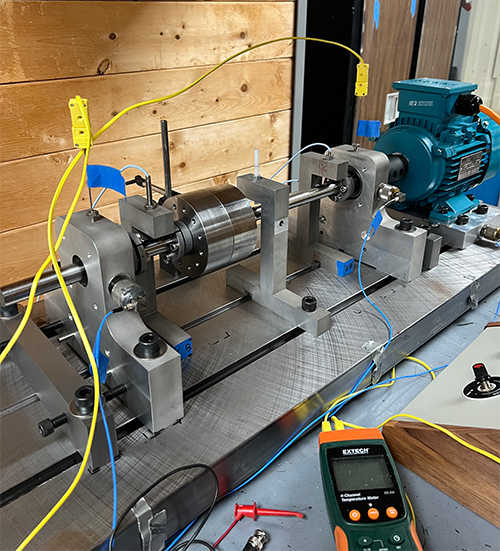
Figure 1: Final Configuration of the Benchtop Vibration Test Rig
The primary goals of this IR&D project are to identify and develop advanced signal processing techniques for troubleshooting transient machinery vibration issues for motor-driven trains. Specifically, the project investigates the use of vibration instrumentation combined with motor current sensors to troubleshoot transient events. A benchtop scale vibration test rig was developed to simulate and detect various transient machinery faults using the developed techniques, as shown in Figure 1.
Accomplishments
The project has identified several time-frequency analysis techniques as promising for application to machinery fault detection and troubleshooting. Continuous wavelets have been identified as the most promising technique through preliminary analysis of a sample transient waveform. Detailed design of the benchtop test rig was completed, and the project progressed to hardware acquisition and rig build up. Once commissioning of the test rig was complete, the rig was used to acquire data for various simulated machinery faults for analysis and detection using the time-frequency techniques.
Initial testing resulted in undesirable vibration levels above 3,000 rpm. The test rig was reconfigured as shown in Figure 1 to reduce sensitivity to shaft runout on the driven end, allowing for data acquisition at speeds up to 4,600 rpm. Testing was conducted with both rigid and elastomeric couplings, with and without intentional misalignment, and varying rotating unbalance levels. Transient vibration signals were captured for several planned conditions, including: maximum acceleration rate startups; maximum deceleration rate shutdowns; short-term mechanical rub events with aluminum, copper, brass, and plastic rods; induced bearing faults; and motor electrical power single and dual phase drop events. The vibration signal time waveforms captured during these conditions are were analyzed using continuous wavelet analysis techniques, which have demonstrated characteristic signatures such as those shown in Figure 2.

Figure 2: Representative Wavelet Processing Output for a Transient Rub Event
A significant set of representative vibration probe and motor current data was captured during the project for various fault and transitory conditions, as documented in the final report. Potential use of this technology, which could be especially useful in conditions involving very short term transients, is being explored with clients as an alternative to more traditional analysis techniques that are generally more effective under steady state conditions.