Background
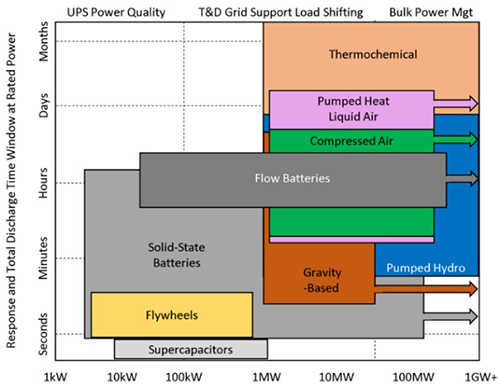
Figure 1: Thermochemical is the most practical pathway for grid-scale storage at seasonal durations.
Many carbon-free energy sources, such as solar and wind power, are often too intermittent to provide reliable, grid-scale power. Therefore, energy storage technologies will be critical in the transition to a carbon-free economy. Compared to other storage technologies, thermochemical energy (i.e., renewable fuels requiring combustion for conversion) is the most practical pathway to providing grid-scale energy storage/dispatch at seasonal durations (Figure 1). Thus, industries and governments are actively pursuing combustion systems that utilize hydrogen (H2), ammonia (NH3), renewable natural gas (RNG), and other alternative fuels.
Approach
Design and test a lower-cost combustor rig: Most combustion tests require the design of a unique combustor and this design effort is often prohibitively expensive. Alternative manufacturing processes are being explored as a means to reduce the overall design and manufacturing costs associated with combustion tests.
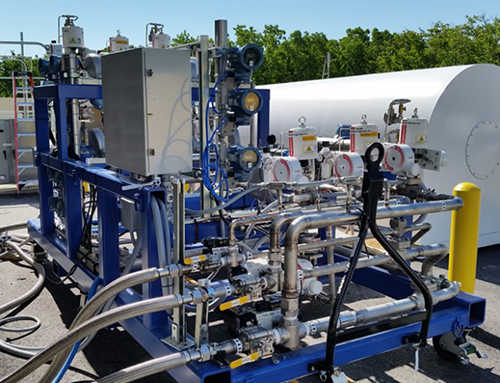
Figure 2: The fuel cart will allow the use of NH3.
Add capability to test with NH3: The existing fuel mixing cart (Figure 2) is used to mix up to four gaseous fuel components (including natural gas and H2) to generate custom fuel blends that mimic various fuel sources. This system is being expanded to include NH3.
Increase access to multiple commercial and government clients: Several key components utilized in the HEAT facility are client owned. Work in this PDIR will either remove the ownership barrier or develop replacement equipment to allow HEAT facility access to a wider customer base.
Accomplishments
- The project team has generated two alternative designs for the combustors. The additively manufactured design will yield roughly 33% to 50% lower manufacturing costs compared to combustors manufactured with traditional techniques. Initial estimates for the cast refractory combustor indicate roughly 80% to 90% lower costs compared to traditional manufacturing techniques. In the coming year, these two combustors will be tested to determine the quality of the data.
- The project team has also successfully negotiated the use of the existing HEAT facility equipment such that this equipment will be available for use by a larger client base.
- Finally, the project team has performed initial sizing and compatibility studies to allow the use of anhydrous NH3 in the fuel blending cart.