Background
The development of immersion grating (IG) spectrographs has moved from an interesting science experiment to production and implementation on several professional ground-based telescopes over the last 20 years. The uniqueness of immersion grating technology is that the diffraction grating is produced out of some transparent (depending on wavelength) crystal (i.e., silicon, germanium, cadmium) whose size can be reduced relative to conventional reflective grating by a factor equal to the index of refraction of the material relative. This reduction in size, while retaining the same performance of more conventional and much larger spectrographs, allows for the development of compact instruments more suitable for balloon or space flight missions where mass and volume are at a premium.
An immersion grating-based spectrograph working at near-infrared to mid-infrared wavelengths requires cryogenic cooling to effectively suppress the background thermal radiation intrinsic to all matter. Additionally, all optical systems require alignment to a fraction of a wavelength to maintain optimal performance. To maintain optical alignment of an immersion grating spectrograph, a thermal control system that maintains sub-degree thermal stability and a mechanical mounting system that maintains sub-micron mechanical stability against system perturbations over observational timescales must be implemented.
The primary objective of this project was to implement tight thermal control of a crystalline immersion grating using a custom-designed optical mount and commercially available thermal controller.
For the instrument design and the wavelengths of interest, the immersion grating is made from silicon. Silicon was chosen as it is transparent at our wavelengths of interest and has a very high index of refraction, which is necessary to minimize the size of our optical system. The index of refraction for silicon is 3.5 at 70-80 K, varies by 50e-06 K-1,and is almost independent of wavelength from 2-5 microns. Since the wavelength, lambda, at a given angle of diffraction is proportional to index dlambda/lambda = dn/n = 5e-05/3.5 = 1.4e-05 K-1 it means that the spectra would shift on the detector by about 1/2 a resolution element for a 1K temperature change. Given that the spectral performance of the instrument is the key to the planned science, a stability on the order of 100mK is needed to keep the spectral dispersion stable to better than 1/20th of a resolution element.
Approach
The approach was threefold:
- Design a mechanical mount that would constrain the immersion grating over thermal deviations.
- Model the thermal performance of the mechanical mount over the required temperature range.
- Finally, using a commercial controller, demonstrate the performance of the design over the temperature range and various time periods and compare it to the thermal model.
Accomplishments
This targeted internal research program developed, built, and tested, at operational temperatures, the grating mount subsystem for SAKHMET. The system met all success criteria by demonstrating better than 60mK stability of the subsystem for durations longer than 1-hour, 6-hours, and 72-hours. Based on what was learned during this research program, this design will be able to be flown on any future suborbital mission with sufficient mass, payload, and power allowances. This research retired a technical risk in our upcoming proposal submittal.
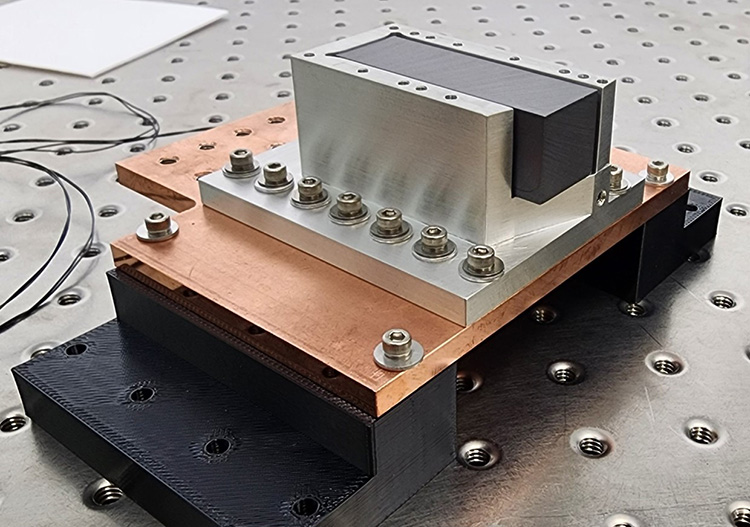
Figure 1: Assembled immersion grating mount. The black feet are 3D printed Delrin. 3D printing for cryogenic applications is now possible due to the use of special vacuum and cryogenic resistant materials.