The no-code development movement describes the proliferation of tools and frameworks that enable people untrained in traditional coding languages to develop useful software. This has become commonplace in the world of web development where people can drag boxes around and use high level tools to control the appearance and behavior of the pages without ever writing a line of HTML or JavaScript. By lowering the barriers to web development, more people and organizations can harness the opportunities of the web. Its value evident, no-code development is spreading to many other software dependent industries, with robotics being no exception.
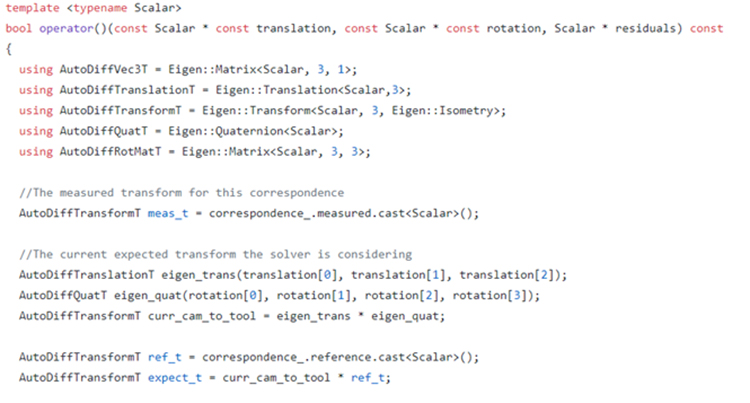
Dense code can be intimidating for people unfamiliar with development languages.
Robots are getting faster, stronger, and smarter. At the same time, they are becoming less expensive and better equipped to do sophisticated tasks. These advances mean that robots have the capacity to do greater amounts of valuable work. However, many robots on our factory floors remain underutilized. One of the foremost challenges in robotics today is offering people ways to get the most out of their robots. This drives higher productivity, wider adoption, and spurs further technological advancements.
Sustaining Robotics Investment with No-Code Development
For most of the history of robots, only highly trained engineers and technicians had the expansive knowledge needed to make the robots do useful things. Today’s robotics landscape is vastly different, a plethora of tools enable people to understand and program a robotic system without ever writing a line of code. By lowering the technical barriers to entry, more people can be involved in the robot programming process. Having more people at the table means that better ideas will emerge and organizations are less reliant on the tribal knowledge carried by a few experts. This has the potential to build sustainability into robotics research, development and education.
Robot manufacturers are understandably among the most motivated to make their systems easier to use. Across the industry, OEMs have made great strides in improving the user experience of working with their systems. Many of them have new teach pendant interfaces, which are more intuitive and lower the educational barriers to entry, while still offering the fine-grained control that many engineers want. These new interfaces enable users to quickly and easily program robots to do different tasks.
Process agility with the ability to make these quick changes between tasks is a huge upside for small and medium sized manufacturers. Many of these smaller companies have little to no experience with robots and investment in a new robotic system is a major decision. However, when these companies can use a single robot to do different jobs, the value is multiplied. They can use a robot to quickly plug holes in their production line in the morning and palletize finished parts in the afternoon.
Robot Motions with No-Code Programming
Southwest Research Institute (SwRI) recently completed an internal research project to develop a method of programming robot motions that doesn’t even require a person to touch the teach pendant. This system, called Visual Programming, enables a person to demonstrate a motion to a robot with a special tool and have the robot be able to reproduce the motion. This no-code programming system needed only a single 2D camera to accurately track the person demonstrating the task to the robot. The minimal cost of the Visual Programming equipment makes it more accessible to precisely the people that would benefit from it most.
Another research effort underway at SwRI focuses on making robots more intelligent collaborators with people. The method being investigated uses SwRI’s markerless motion capture technology to continuously collect data about a person’s position to predict collisions between the robot and the person. The robot then replans its motion on the fly to avoid a collision. From an operator’s perspective, this technology is invisible, however its results are certainly tangible. Operator safety and process efficiency both win with this capability.
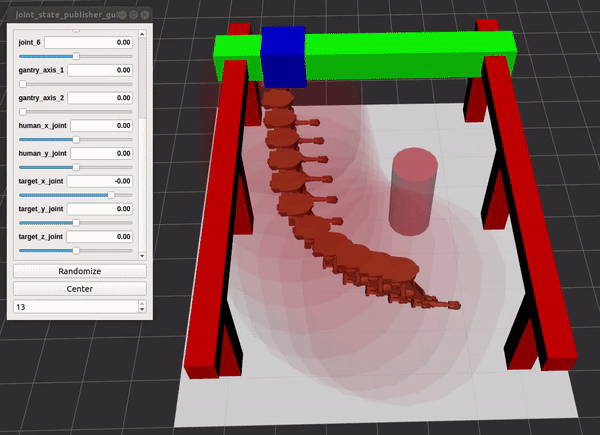
This image depicts how a robot can predict collisions between robots and humans.
One last area where the barrier of coding is crumbling is in system monitoring. Typically, a software developer must design and build a custom human-machine interface (HMI) for a complex system. These can be difficult to make changes to and require elaborate code deployment schemes. There has been a renaissance in web browser-based interfaces for robotic systems. These are particularly appealing because web browsers are a familiar and widely supported platform. These tools enable engineers and operators alike to see how their robot is understanding the world, aiding in the development, operation, and troubleshooting of robotic systems.
To Code or Not to Code a Robot?
Robots are quickly becoming capable of performing previously unimaginable tasks. Our SwRI staff is intently working on new capabilities and solutions so that everyone can fully leverage these pieces of equipment. Improvements to native robot interfaces are a great starting point, but the needs of manufacturers are constantly evolving, so the interfaces of tomorrow are what our team is building today. The R&D environment is staying nimble, listening to the pain points of users, and leveraging the latest technology to build new no-code development tools that help manufacturers of all sizes thrive.
To learn more, visit Intelligent Manufacturing & Process Solutions or Contact Us for a demonstration.
