In this article, the first in an occasional series on machine learning, we are going to discuss algorithms and automation tools developed by Southwest Research Institute to detect, quantify, and categorize methane leaks.
The Innovations in Automation Blog typically covers SwRI automation technologies that enhance robotics, manufacturing, and industrial applications. Through automation, particularly with machine learning, we are also enabling breakthroughs in a broad spectrum of environmental, health and safety challenges.
Finding Fugitive Methane Emissions
Pinpointing the fugitive sources of methane, a constituent of natural gas, is an important first step in mitigating environmental and safety hazards.
There’s also the matter of quantifying a particular leak and determining whether the source is biogenic, such as livestock and melting permafrost, versus anthropogenic, such as flaring from oil and gas production or a leak on a remote natural gas pipeline.
The Environmental Protection Agency (EPA) regulates fugitive methane emissions, which creates a need for companies to conduct routine inspections. As such, there is a significant need for robust technologies to provide early indication, quantification, and sourcing of an unexpected emission.
Optical sensing combined with machine vision algorithms provide an indirect methodology. Through internally and externally funded research, SwRI has developed the Smart LEak Detection (SLED) system, fusing optical gas imaging, infrared cameras and other sensors to detect and analyze methane leaks.
SwRI has over 60 years of heritage in the oil and gas industry, providing testing and evaluation of techniques, pipeline equipment, and third-party evaluation of leak detection and repair technologies. Our expertise includes fluids engineering and research and development of natural gas machinery and pipeline infrastructure. In addition, SwRI has experience in simulating, measuring, and collecting data on various oil and natural gas pipeline leaks. Furthermore, SwRI has over 20 years of experience in computer vision and machine learning algorithm development for complex and safety-critical inspection tasks.

Fugitive Emissions Testing Webinar
Jacqueline Manders discusses the standardized fugitive emissions qualification procedures for valves, the challenges associated with fugitive emissions testing, and the methods used to address those challenges, emphasizing safety and data quality.
What is Methane Gas?
Methane is a colorless, odorless gas that occurs commonly in nature. Its chemical formula is CH4, a member of the paraffin series of hydrocarbons, and a potent member of known greenhouse gases. Now that you have a good understanding of what it is, let’s discuss the challenges of detecting and quantifying methane.
Where can we find Methane gas?
Methane leaks can occur near valves, compressors, and pipelines where natural gas is gathered, transported, or distributed. It is a common “fugitive emitter,” which typically means gas leaks from a pressurized environment ranging from underground systems to heavy industrial equipment. Methane can also be found normally in nature. It’s produced by the anaerobic decomposition of vegetable matter and is also produced by animals such as cows and even termites.
While methane is hard to see, it is important to keep track of where it is in the world. Long-term undetected methane leaks can lead to serious environmental and safety hazards due it being a flammable greenhouse gas.
How do you Detect Methane?
Older technology used “sniffer” techniques that required instruments to be placed directly in the path of methane to detect and determine concentration levels. This process was laborious and made it difficult to accurately find the source of fugitive emissions. Operating a sniffer is hazardous to humans because it requires close interaction in methane rich environments.
Currently, methane leaks are detected by routine manual inspections which survey methane-energy plants with optical gas imaging (OGI) capable cameras. An OGI is similar to a video camera that operates in the midwave infrared (MwIR) band (methane band), allowing operators to scan a site from a distance and visualize the otherwise invisible methane gas. It is important to note that methane is several times more absorbent than Carbon Dioxide (CO2) and Nitrous Oxide (NO2), other prominent chemicals in this band that make the midwave spectrum optimal for detecting methane. Methane is invisible to the human eye, but in the midwave band methane energy is absorbed, making it appear as a smokey gray/black plume in the image. OGI cameras are expensive, and methane is still difficult to see in the midwave spectrum, thus special training for camera operation is required for methane plant inspectors.
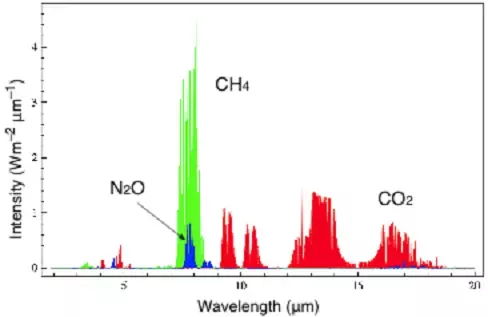
This graphic depicts how Methane (CH4), carbon dioxide (CO2) and Nitrous Oxide (N2O) appear on the midwave infrared spectrum. SwRI uses midwave infrared (MwIR) to detect methane emissions with its SLED system.
One of the problems with inspection using OGIs comes from motion. Detecting methane from a single static image is difficult. Even with the methane absorbing energy, it can appear translucent on an OGI image and blend in with its surroundings. One of the best ways to find a leak is by observing the methane’s motion in the image(s) relative to everything else that is static in the image. This problem is exacerbated by the fact that inspectors are typically using these cameras by hand, or more recently, on an unmanned aerial system (UAS) platform. This makes spotting a methane leak a difficult task, without stopping and staring at any given component on a site. To help in improving the efficiency and reliability of methane inspections, SwRI partnered with the Department of Energy’s National Energy Technology Laboratory to apply machine learning and deep learning tools to this space.
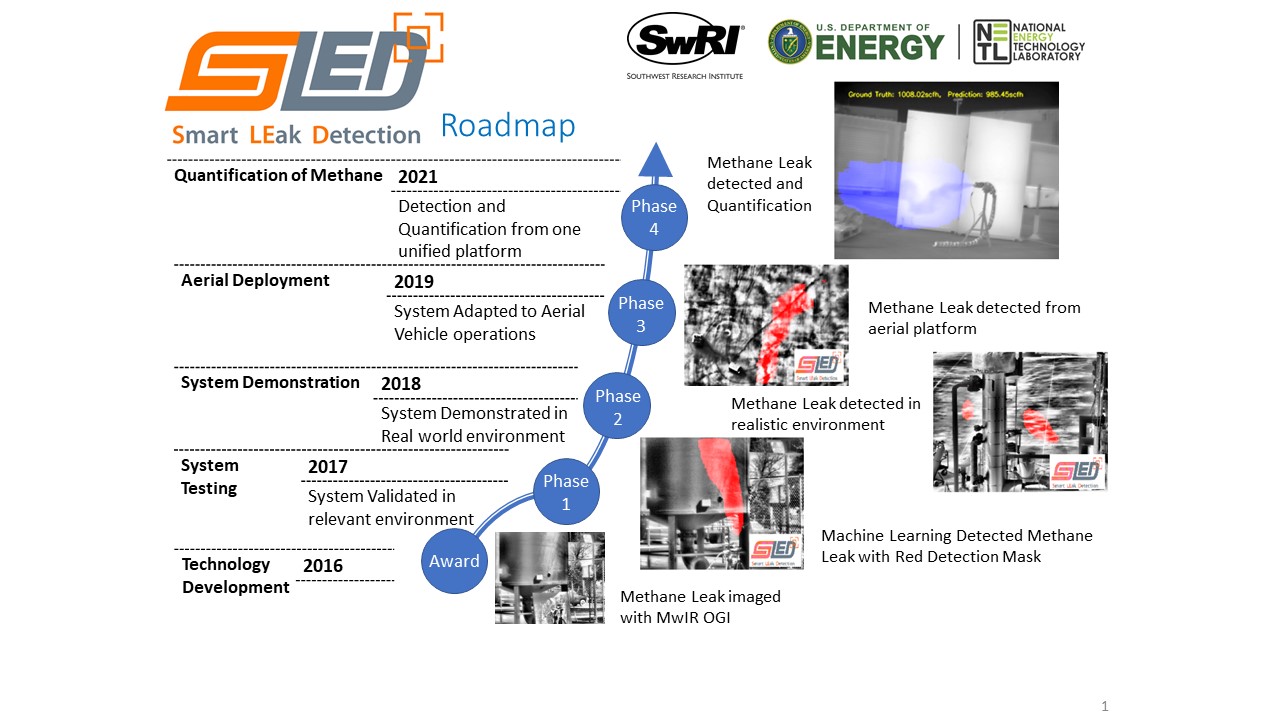
R&D timeline of Smart Leak Detection (SLED), a tool developed by SwRI to detect liquid hydrocarbon leaks and gaseous leaks of methane.
SLED/Methane, or SLED/M, advances the state-of-the-art methane emission detection and quantification by focusing on three key critical criteria for effective methane emission mitigation:
Autonomy (no need for a human to be in the loop)
High reliability (low false alarm rates)
Real-time performance.
Once a camera has been deployed, SLED can supervise the field of view forever, and let operators know when a leak has been detected. It can reliably identify and alert on leaks, and not get tricked by motion in front of the camera or other common occurrences due to the robustness of training in our models. SLED is real-time, meaning that operators are notified the moment it detects a methane leak. These principals allow SLED to be one of the most advanced automated methane detection methods out there, and its capabilities are still growing.
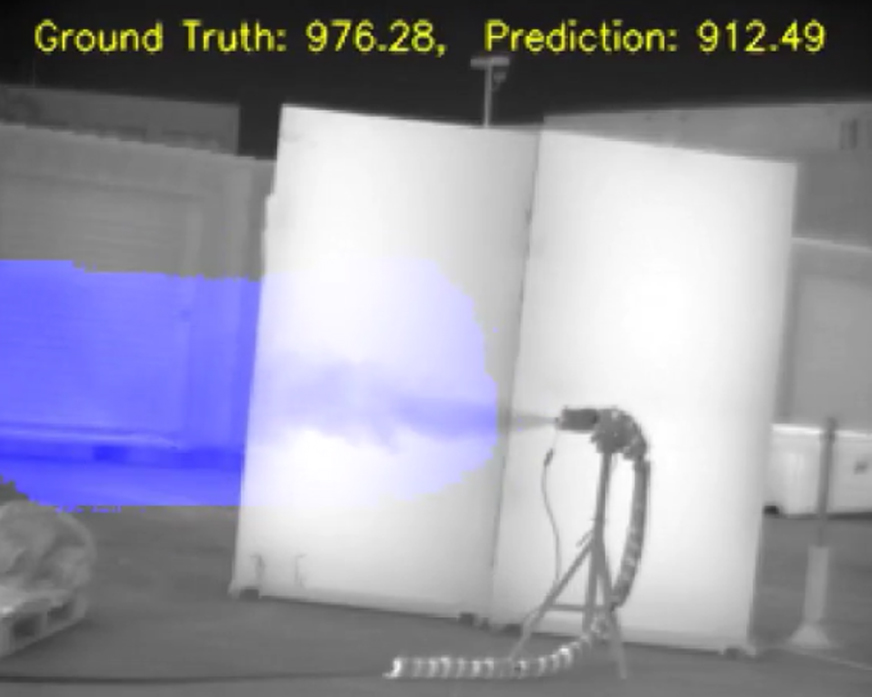
A plume of methane is visible in blue, representing methodologies used to quantify methane leaks.
Today, Southwest Research Institute is working on expanding SLED’s capabilities by investigating automated detection via unmanned aerial vehicle, or drone, imaging and quantification of methane leaks, and its generalizability in different environments. Drone imagining produces a unique challenge of needing to stabilize the image before passing it through our algorithm, which further complicates methane detection by emphasizing the difficulties of properly handling motion.
Quantification of a methane leak has shown success as we can reliably quantify the rate of the leak within 50scfh by further advancing our algorithm that takes in OGI image information. The level of absorption of methane in the midwave band helps our models not only detect, but also quantify the leaks. We also want to generalize SLED by testing it in different environments such as ice and snow. Many methane planes operate in cold weather, and we intend to prove SLED’s ability to handle a variety of different environments.
Want to learn more about SLED?
SLED is a state-of-the-art methane leak detection algorithm whose capabilities are ever-growing. It is important to realize that there are many special cases, unique environments, and technical difficulties in automating methane inspections, and SLED aims to conquer them all.
To learn more about SLED, contact Heath Spidle, a research engineer in SwRI’s Advanced Inspection Systems section.
For more information, visit Methane Leak Detection and Fugitive Emission Testing.