Ever since the Wright brothers flew the first motor-powered airplane in 1903, humanity has been trying, and succeeding, to fly faster and faster. However, as aircraft speeds increase, the physics of high-speed flight imposes challenges that must be overcome. Breaking the sound barrier, or flying faster than the speed of sound, is one example. The speed of sound is a critical measure that affects a vehicle in flight, which is specifically associated with the physical properties of air.
The speed of sound in air is roughly 740 miles per hour, referred to as Mach 1, though it changes depending on the specific composition and temperature of the air. In the early years of human flight, clocked speeds were well below Mach 1. It took nearly half a century of engineering development before an aircraft was able to breach the sound barrier. This metaphorical hurdle refers to sudden increases in aerodynamic drag and other undesirable effects aircraft experience as their speed in air approaches the speed of sound.
In 1947, the Bell X-1 was the first official aircraft to break the sound barrier during level, controlled flight. This pioneering event demonstrated an understanding about supersonic flight and shock waves that form in the air when the aircraft exceeds the speed of sound as well as how compressed air behind the shock waves affects vehicle dynamics. The next two decades witnessed continued progression of supersonic aircraft through the SR-71, which could fly at Mach 3, and the X-15, which used rocket propulsion to reach sustained flight at Mach 6. More recent unmanned test vehicles, such as the X-43 (1997–2004) and X-51 (2004–2013), have demonstrated the feasibility of non-rocket-based propulsion methods, including scramjets (supersonic combustion ramjets). A scramjet has a novel combustion chamber — where the air is mixed with fuel and ignited — designed to operate with supersonic airflow.
ABOUT THE AUTHORS
Dr. Nicholas Mueschke (left) is a principal engineer in SwRI’s Engineering Dynamics Department. He has extensive experience in fluid dynamics, turbulent flows, computational fluid dynamics (CFD) and is the author of SwRI’s CULEBRA CFD code, which includes chemistry for modeling blast effects and hypersonic aerothermodynamics. Dr. James Walker is director of the Engineering Dynamics Department and an Institute scientist. Walker is an expert in impact and penetration mechanics and material response under extreme conditions. A large team of SwRI scientists and engineers are involved in new hypersonics initiatives.
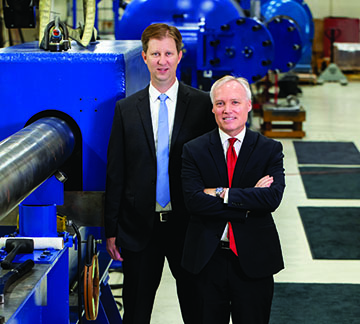
While earlier test programs demonstrated the possibility of hypersonic aircraft operating in excess of Mach 5, the U.S., China, Russia and other countries are all striving to develop the first operational hypersonic systems. Aircraft and missiles that can cruise and maneuver at five times the speed of sound or faster will offer significant military advantages. In the commercial arena, a hypersonic flight could travel from New York to Los Angeles in less than 30 minutes, blowing away today’s subsonic airliners covering the same distance in 5 hours. The demand is there, and the technology is coming.
Southwest Research Institute is using its unique facilities and capabilities to explore how hypersonic flight in excess of Mach 5 differs from supersonic flight at lower Mach numbers. The complexity of the engineering challenges associated with hypersonic flight requires creative problem-solving as well as advanced modeling and testing.
Environmental Extremes
As an aircraft travels faster and faster, the air around its nose cone, wing leading edges and air intakes can easily heat to temperatures hotter than the surface of the Sun (approximately 5,800 K or 10,000° F). As temperatures increase, air molecules can dissociate or ionize. These hot atoms and ions are prone to chemically react with anything, including the vehicle surface they surround.
DETAIL
Ablation is the removal or destruction of material from an object by vaporization, melting or other erosive processes.
Friction heats the air around an aircraft to the point that its outer surface begins to melt, vaporize, oxidize, erode or ablate away. This is not the only problem encountered at hypersonic speeds. It does, however, embody the grand challenge of hypersonic flight: How do you design a vehicle to survive an environment so harsh that the vehicle can literally disintegrate during flight? Because of these high temperatures, all hypersonic vehicles are outfitted with “thermal protection systems.” These special materials or coatings protect vehicles from high temperatures and include silica thermal tiles on the space shuttle and X-51, titanium alloys on the X-15 or carbon-carbon composites on the X-43. For example, Apollo capsules were coated with an ablative material that vaporized during reentry, absorbing the heat from the air, like evaporative water in swamp coolers, protecting the capsule from rising temperatures. The hottest parts of the space shuttle, the nose cone and the leading edges of the wings, were made with specially coated carbon-carbon composites that can withstand extremely high temperatures without melting or ablating.
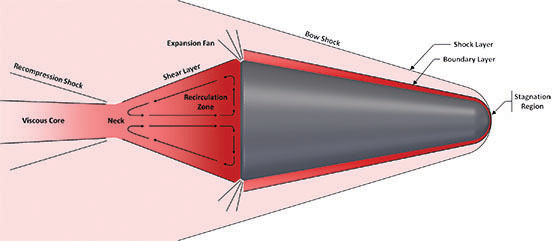
This figure illustrates the aerodynamics of a hypersonic body in flight.
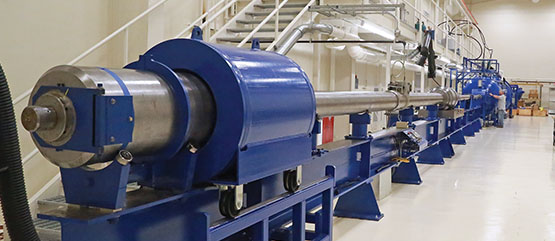
SwRI offers a 7,050-square-foot facility for launching projectiles at high speeds. The centerpiece of the facility is a two-stage light-gas launcher that can achieve velocities approaching 15,660 miles per hour.
Surfaces and structures must deal with extreme aerodynamic pressures and external temperatures while keeping internal structures and electronics cool. Aerodynamic and thermal protection systems must tolerate aerodynamic forces and thermal expansion of materials so extreme that they can actually change the shape of the aircraft during flight. Propulsion systems must survive extreme thermal and shock conditions while maintaining combustion stability. Communication and guidance systems must negotiate a potential sheath of charged particles engulfing the vehicle in flight. These issues all affect and complicate the vehicle design.
DETAIL
An airbreathing engine such as a jet engine or scramjet engine sucks air in the front and pushes it out the back very quickly.
Ultimately, for aircraft to fly at hypersonic speeds for sustained durations, it is necessary to understand the heating that occurs and how it affects the performance of engineered materials and structures. Airbreathing propulsion systems at hypersonic speeds (such as scramjet propulsion systems) complicate matters even more. SwRI has been developing tools to understand the shock waves, flows and chemistry of hypersonic flight and the material systems needed to survive those conditions.
Hypersonic Flight in the Lab
Reproducing the extreme velocities, temperatures and chemistries of hypersonic flight is extremely difficult. Flight tests are the only means of replicating such an environment — but are cost-prohibitive. Hypersonics researchers must use ground test facilities to recreate critical aspects of flight conditions. Ground-based facilities, such as wind tunnels, can selectively match some flight conditions, but only for milliseconds to seconds at a time. Currently, no single test facility can replicate all aspects of hypersonic flight.
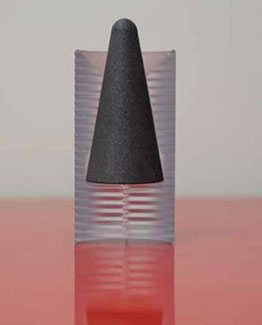
For light-gas gun testing, SwRI encases spherically blunted conical test projectiles in a sabot, a structural device used to keep smaller projectiles in the center of the barrel when fired. The sabot separates from the projectile and is stripped away when it hits an impact plate.
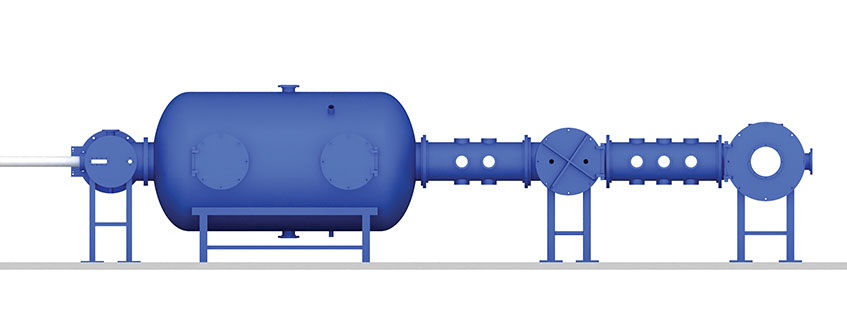
SwRI’s light-gas gun flight range includes multiple portals in the flight tubes to allow sophisticated high-speed imaging of hypersonic flight experiments.
At SwRI, researchers are using a large two-stage light-gas gun to explore how to replicate hypersonic flight. This facility can launch scale-model flight vehicles at speeds from Mach 5 (1.7 km/s) to Mach 20 (7 km/s) into controlled atmospheres that are quiescent or “quiet,” meaning gas is at rest, with no acoustic noise present to inadvertently introduce turbulence. The constraint with this approach is that flight vehicles are small-scale models. They traverse the flight range in only a few milliseconds and are not recovered.
One advantage of testing in the SwRI light-gas gun is the atmospherically controlled environment. Flight range pressure and gas composition can be controlled to mimic atmospheric conditions equivalent to up to 27 miles in altitude. This allows SwRI to replicate flight conditions for a range of different flight systems, including the space shuttle to ballistic missiles and everything in between.
Small-Scale Flight Testing
Launched projectile experiments explore different aspects of hypersonic flight physics, such as the shock wave geometries around and within the vehicle and the chemical reactions resulting from extreme temperatures. Multiple viewports along the flight path allow high-speed flash X-ray, high-speed video, schlieren imaging and photonic Doppler velocimetry, which measures velocities in dynamic experiments with high temporal precision. SwRI is also developing new diagnostic tools to study light emitted by different chemical species created in the high-temperature flight environments, including emission and absorption spectroscopy, and additional laser diagnostic techniques.
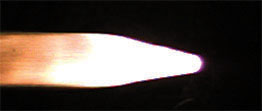
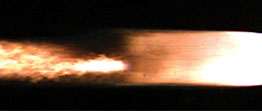
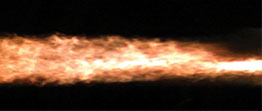
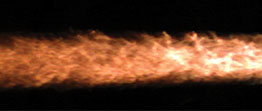
This high-speed video sequence shows a spherically blunted conical test article in flight at Mach 14.8 (11,400 mph), illustrating hardbody and wake signatures. The flow around the vehicle and in the wake in these images is self-luminous due to the high temperatures created by the hypersonic flight. No external lighting was added to take these pictures.
Some experiments examine how to use the flight range to observe the aerodynamics of different geometries in flight at very high Mach numbers. Understanding the chemistry of the local gas around the vehicle is paramount in the selection of materials that can survive this thermal and chemical environment, understanding vehicle aerodynamics and control, and the design of any airbreathing propulsion system and communication systems. Another goal of these experiments is to understand how the chemical environment interacts with material shed from the vehicle to produce a visible and infrared light-emitting shroud of gas around and in the wake of the aircraft.
DETAIL
Schlieren photography (from German for streak) is a visual process used to photograph the flow of fluids of varying density. Invented in 1864 to study supersonic motion, the technique is widely used in aeronautical engineering to photograph the flow of air around objects.
Observing the object in flight requires non-contact optical diagnostics, so every test is recorded using high-speed video. This provides raw images of the test article in flight and records the observed chemical luminescence. If gas temperatures are sufficiently hot, ablated material shed by the test article is sometimes visible. However, certain features of the flow field are not easily visible, such as shock waves and density fluctuations in the air around the flight body. Using specialized collimated light sources, SwRI amplifies and visualizes diffraction caused by light rays passing through changes in air density. These shadowgraph or schlieren images, depending upon the exact method used, directly image the test article, shock waves and turbulent zones and can, at times, allow quantitative analysis.
SwRI is also using internal research funding to develop advanced optical diagnostics based on the light emitted by excited chemicals around a flight body. Engineers use this emission spectroscopy method to identify and quantify the specific chemical species present in the flow field. SwRI engineers are developing advanced diagnostic tools with Dr. Christopher Combs at the University of Texas at San Antonio (see related Connect article). These laser-based methods use a specific wavelength to selectively excite different molecules, which subsequently fluoresce in predefined colors as they release the energy absorbed from the laser. Lighting a small packet of gas in this way allows engineers to track its movement around the flying object. These techniques can provide detailed measurements of velocity, density, temperature and chemical species concentration.
One challenge with using a ballistic system to launch and study hypersonic flight is the intrinsic limitation on the scale of the test article that can be flown. SwRI is researching how to manipulate the gas pressure and chemical composition of the flight range to better correlate the small-scale tests with full-scale hypersonic aircraft flight conditions. To design these experiments and understand the physics of the flow where measurements cannot be made, engineers leverage computational fluid dynamics tools. High-fidelity simulations run on hundreds of central processing units performing advanced calculations to predict shock wave locations, local gas temperatures and how air components break down in the highly energetic environment around the test article. This information guides the development of optical diagnostics and test analyses.
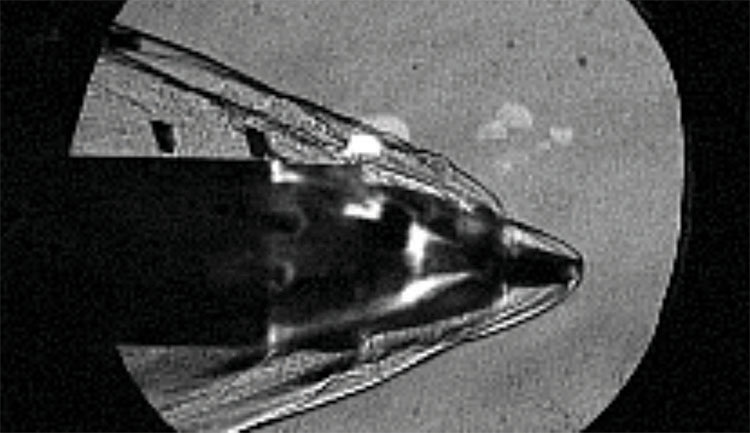
This schlieren image of an additively manufactured test article with internal ducted ports for air flow shows an experiment conducted at Mach 9.6 (7,400 mph).
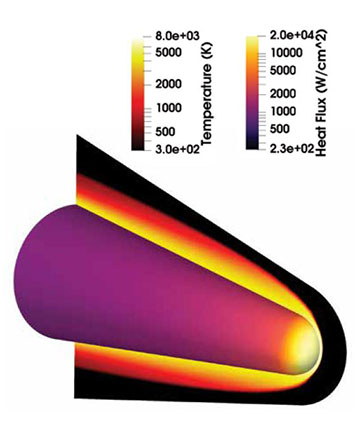
High-fidelity computational fluid dynamics simulations of a small-scale test article flying at Mach 14.8 (11,400 mph) predicts gas temperatures behind the shock wave reach temperatures in excess of 5,000 K (8,540° F). At these temperatures, air molecules break down and form new chemical compounds, such as nitric oxide.
In addition to using a government-generated aerodynamics code specifically designed for hypersonic aerodynamics, SwRI has developed a computational fluid dynamics code that specializes in solving transient flows with strong shocks and complex, transient chemical reactions between numerous gas species. Known as CULEBRA, this tool is tuned to the complex chemistry and transient flow features that occur behind strong shock waves, like the bow shocks that develop in hypersonic aircraft.
Airbreathing Hypersonic Flight
DETAIL
Engineers named its CFD code CULEBRA, which means snake in Spanish, in homage to SwRI’s location on Culebra Road in San Antonio.
The hypersonics research community is particularly interested in airbreathing engine-powered flight, such as that provided by scramjet propulsion systems. Conceptually, these engines are very simple. With no moving parts, air is forced through an engine duct at supersonic speeds where the fuel is injected and ignited, and the exhaust products expand to generate thrust. However, the complex shock wave structure and shock wave-boundary layer interaction, combined with the supersonic combustion, require immense structural cooling. SwRI test techniques examine the shock waves as they interact with complicated shapes. Quantitative details of how a series of shock waves form inside a flight body are very important for scramjet engines. Researchers are investigating ways to build scale models of transparent flight bodies with inlets and internal ducts and using imaging techniques to see the details of the internal shock structure. Though these transparent materials do not survive an extended flight test (because they melt and ablate), they maintain their shapes for the few milliseconds of flight in the light-gas gun flight range, allowing researchers to image the shocks inside the body to understand where they are and how they interact. Engineers then use a variety of aerodynamic, reactive flow and shock/impact physics codes to better understand these complex interactions.
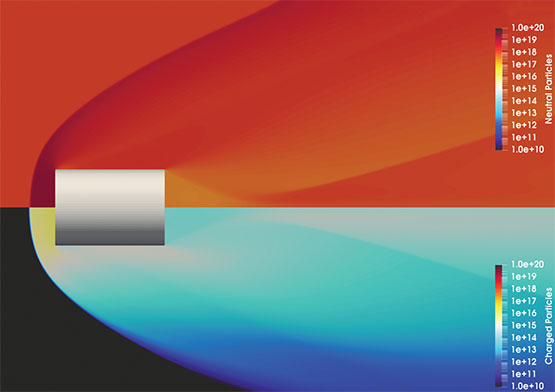
SwRI-developed CULEBRA models of a cylinder in flight at MACH 16 predict that extreme temperatures strip electrons off molecules and a sheath of plasma forms around the flight body.
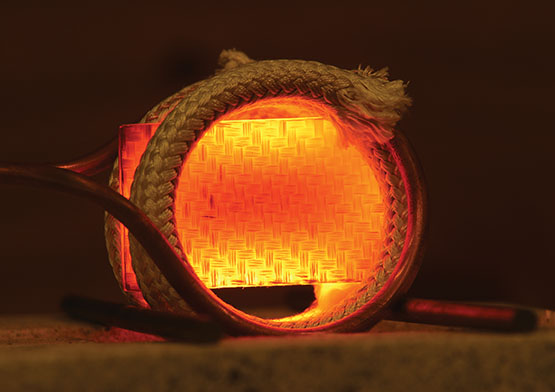
As part of its hypersonics research, SwRI is conducting high-temperature materials testing of carbon-carbon composites, shown glowing at 2,000° F.
Tomorrow’s extended hypersonic flight goals are substantially different from current atmospheric reentry vehicles, which experience hypersonic flight environments for a relatively short period of time. Hypersonic airbreathing vehicles intended for civilian air transport and military applications need to maintain hypersonic flight for minutes to several hours. Achieving this performance requires detailed understanding of the thermal environment the materials need to survive as well as a complete understanding of fuel efficiency and scramjet effectiveness.
High-Temperature Materials Testing
SwRI is also exploring other avenues of hypersonics research and development, particularly the response of advanced materials to extreme temperatures and loading rates. As new material systems are developed to withstand extreme flight environments, engineering design tools require information on how these systems behave at different temperatures and under varying load configurations and rates. SwRI has a long history of developing test methods to acquire the data as well as the subsequent material models that use the data.
In recent years, SwRI has expanded the range of strain rates and temperatures that can be achieved in various mechanical and impact tests. SwRI uses induction heating techniques to heat carbon-carbon composite materials to 2,670 K (4,350° F) and laser-based heating to rapidly heat test specimens to above 2,600 K (4,220° F).
New materials, and especially high-temperature ceramics and composites, will play critical roles in the functionality of hypersonic vehicles. Extreme temperatures represent only half of the equation for hypersonics materials testing. Mechanical, impact and high strain rate failure testing must incorporate the effects of materials in thermally excited states. Hypersonic designs must incorporate the material expansion, changes in strength and heat conduction as a function of temperature or face the risk of failing in flight testing, an expensive possibility.
An international race to develop operational hypersonic systems is underway with a focus on both airbreathing and boost-glide systems. SwRI’s broad hypersonics research and development activities are improving the understanding of this unique flight environment, how materials and structures respond to it and how those insights can be leveraged to advance current flight system capabilities and reliability.
Questions about Hypersonics Research? Contact James Walker or call +1 210 522 2051 or contact Nicholas Mueschke or call +1 210 522 5128.