The typical person probably doesn’t wake up in the morning with an idea to build a 20-ton robot, standing five stories, wielding a 20 kW laser, and yet we did exactly that with the Laser Coating Removal Robot (LCR). This post, unfortunately, will not discuss the enormous robots you see in sci-fi movies. Instead, it covers large-scale industrial robots intentionally designed for manufacturing, construction, and other large workspace applications.
Industrial robots come in all different shapes and sizes depending on the intended use and application. One of the most common industrial robots features a standard six-axis robotic arm with an approximate 1.5-meter reach, which works well for a range of applications. But once the application drives the need for robots to become very small or very large, there are typically no commercially available robot products or solutions available. Southwest Research Institute develops and works with the traditional six-axis solutions, but we also specialize in custom large robotics for new and unaddressed applications.
Industrial applications have a wide array of requirements and needs as such, hardware is often sized appropriately. The graphic below is a visual representation of the size of the robotic hardware. Smaller crawling or flying robots are typically on the order of several pounds while our largest robots are more than 60 tons.
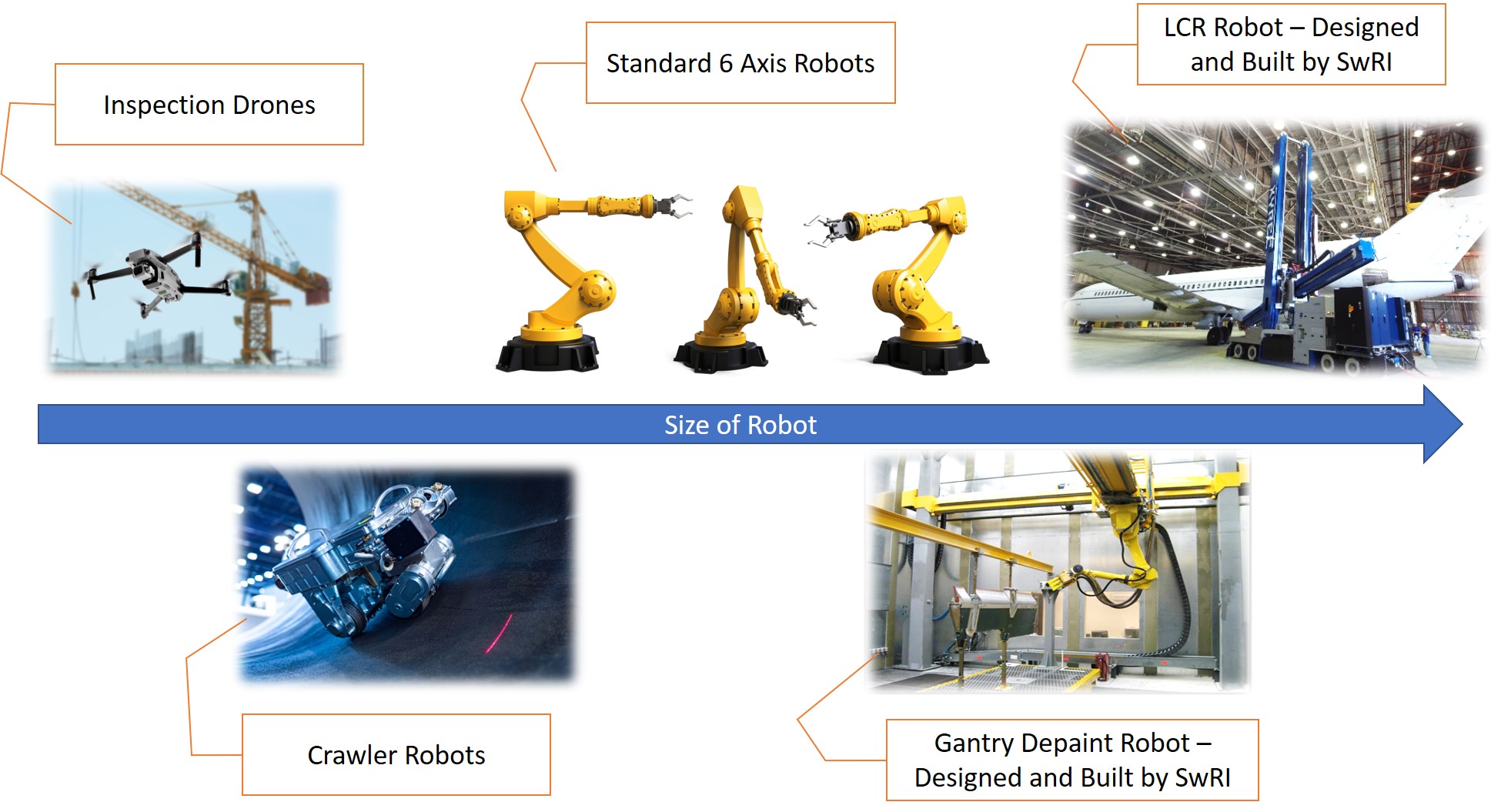
The Case for a Massive Robot
You might wonder why we would build large robots. For us and our clients there are very compelling reasons beyond the coolness factor. In the case of the LCR, we needed to help our client develop a solution to address the full range of aircraft sizes, coatings, colors, and substrates on a broad range of defense and commercial aircraft, from fighter jets and helicopters to cargo planes.
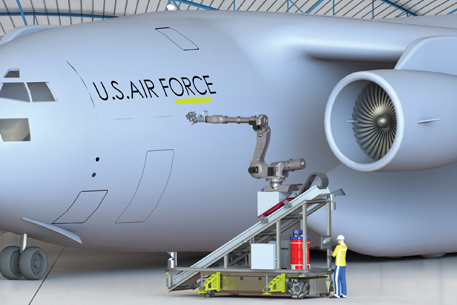
Mobile sanding robot with extended reach.
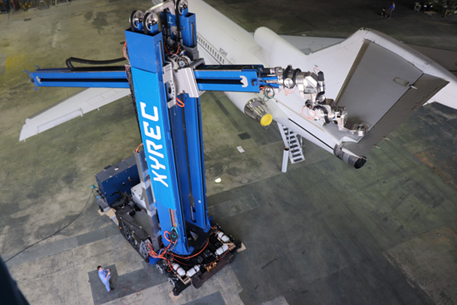
Laser Coating Removal Robot (50 feet tall).
When addressing the reach requirements and process integration for the largest aircraft, which can stand nearly 100 feet tall with wingspans more than 200 feet, an aircraft-sized robot was the leading solution. There were several possible approaches but, in the end, the requirements necessitated a giant mobile robot.
Here are some key aspects to consider when looking at a large workpiece:
- The application is simply larger than standard robot reach:
- Many objects in industry are much larger than the standard robot reach.
- Complex geometry of workpieces may require more axes or flexibility to access.
- Surface crawling robots may not be appropriate for the manufacturing process:
- These robots are typically lower capacity and cannot support high payload processes.
- The process will not allow surface contact.
- Special requirements of precision, positioning, or process delivery:
- Robots are inherently precise and better suited than traditional processes.
- Robots can articulate objects or deliver a process in ways not possible with a crane or forklift.
Now that we’ve discussed some of the reasons why a large robot is the right solution, let’s see what it takes to build such a robot.
Multidisciplinary Teams for Large Robots
A robot like this cannot come together with a small team of industrial robotics specialists alone, and that is where being part of a place like Southwest Research Institute (SwRI) really gives us an advantage. SwRI has expertise in a range of disciplines and processes. Our business areas span advanced science and applied technology from deep sea to deep space. Leveraging the full SwRI Market Segments and expertise is key for our industrial robotics group. Our flexible teaming approach enables our robotics engineers to consult Institute experts on the Mechanics & Materials necessary to hold a robotic arm 50 feet in the air. Or the manufacturing process may require a special coating best understood by Surface Engineering. Bringing in the right subject matter experts for the application reduces cost and risk for our clients.
Construction poses another application for large robotics. The video below demonstrates SwRI’s ongoing research into large-scale 3D concrete printing, which leverages the Institute’s expertise in robotics and Additive Manufacturing.
Beyond having access to a wide variety of subject matter experts, our team is motivated and driven to solve problems. We leverage the latest developments in robotics software and when that isn’t available our team develops custom solutions to meet the unique needs of our clients. Some environments would focus on all the hurdles and roadblocks, instead our team uses a development mindset to try to figure out approaches that would allow us to succeed. Of course, we complete thorough risk assessments and mitigation strategies, but we think more about “How might we” in place of “We can’t because.”
Finally, we have the benefit of world class large facilities, including the Heavy Article Test Facility with the aircraft sanding robot featured in this DECODED(link is external) episode about open-source robotics.
Before a robot ever arrives at a client site, we can use our own facilities to prototype and test our robots, so they are fully evaluated against requirements before they arrive at the client site. That way the client does not need to spend precious time and money while we work out the inevitable bugs of a first time run.
What ideas do you have that requires a large robot?
