Background
Southwest Research Institute (SwRI) utilized a previously developed patented high pressure fluidized bed (HPFB) reactor to test and convert municipal solid waste (MSW) to renewable fuels and chemicals. Moreover, the accumulation of solid waste, increasing cost of landfills, and unrealized value potential of waste feedstocks makes the conversion of waste to fuels very attractive. This collaboration with the City of San Antonio (CoSA) facilitated the evaluation of local MSW as pyrolysis feedstocks in the HPFB system. SwRI evaluated the conversion of different feedstocks to determine potential target fuel ranges that can be expected. The leftover solids will also reduce the volume of MSW to be sent to landfills, as required by CoSA. The efficient conversion of milled MSW due to its amorphous composition and the modularization of the reaction system will be the main challenges to be tackled during this work. Data from these studies informed a preliminary technoeconomic analysis (TEA) and process simulations to determine estimated cost of deployment.
Approach
Ten runs were conducted in the HPFB system, with varied temperatures and feedstock composition. Pyrolysis gas was characterized by gas chromatography (GC), while pyrolysis oil composition was determined using gas chromatography-mass spectroscopy (GC-MS). Yields of each product were determined, and performance was compared based on product composition and quantity. This data was used to assist in a material balance for a conceptual commercial scale facility. Finally, a combined biocrude was hydrotreated in a batch reactor, and the resulting product was analyzed for heteroatom impurities (N, O, S) as well as assessed using simulated distillation for composition.
Accomplishments
Alongside exploration of feedstock effects on product composition, several iterations of solid feeding mechanisms were tested on the HPFB. Given the challenges in preventing pressure leaks and irregularity of solids in MSW, a lock hopper mechanism was added in place of a plastics extruder to allow for greater fractions of non-plastic waste to enter the process. Six feedstock blends and operating conditions were fully characterized. It was determined through the resulting TEA that scale-up of the HPFB system to meet a plant capacity of 20.8 million gallons pyrolysis oil/year, which consumes 100% of San Antonio’s usable annual waste, would result in a capital cost of $20.7 million, with additional costs associated with upstream processing of waste and downstream separation of products. Use of a flexible fluidized-bed system could allow for simultaneous pyrolysis and hydroprocessing of waste, reducing plant footprint and improving process intensification.

Figure 1: HPFB Reactor system, with pressurized lock hopper feeder.
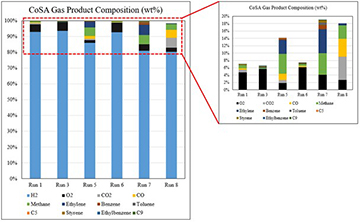
Figure 2: Pyrolysis gas compositions from selected runs.
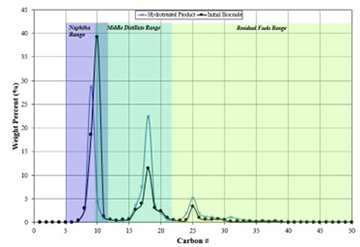
Figure 3: Simulated distillation (ASTM D2887) results for biocrude and hydrotreated product.