Background
Equipment used in environments with ignitable atmospheres, such as refineries and petrochemical plants, must comply with certain standards to avoid the possibility of explosion. One widely used internationally accepted standard is the International Electrotechnical Commission System for Certification to Standards Relating to Equipment for Use in Explosive Atmospheres (IECEx). To produce equipment that is IECEx rated, the manufacturer must work with an IECEx Test Lab (ExTL) and Certifying Body (ExCB) to first have an IECEx Test Report (ExTR) issued for the design. This ExTR compares and tests the design against relevant IEC standards, ensuring it operates safely without posing an ignition risk. In a previously funded project, the Sensors Systems & NDE Technology Section designed and prototyped a novel, low power, intrinsically safe (IS), ultrasonic system to provide precise pipe wall thickness monitoring using existing cables and sensors. IS systems are defined under the IECEx standard as low energy systems that cannot produce an ignition spark. This goal was challenging because commercially available ultrasonic systems for wall thickness measurement generally use short duration high voltage (order of 100 V or greater) pulses to excite the sensors. The goal of this project is to work with an ExTL/ExCB, LabTest Certification, to modify that previous design to obtain IECEx certification, to allow SwRI to develop the capability to design specialized sensors for use in hazardous locations.
Approach
The technical approach to obtain accurate wall thickness measurements is to use a low voltage (8Vpp) chirp waveform with gradually increasing frequency content, and a matched filter comparing the transmitted pulse to the received pulse to perform pulse compression. In addition, an Intrinsically Safe Barrier Board was designed to separate non-intrinsically safe components inside of a flameproof enclosure from signals sent along cabling located in the hazardous environment. This board was custom designed to operate at the frequencies used in ultrasonics.
Once the system design is finalized, the ExTR process requires multiple items to be completed. Physical testing of the system must be carried out, which for this system included tests of the intrinsic safety barrier board, batteries, and thread sealant, as well as determination of the steady-state operating temperature of the system, its response to mechanical impact, and its ability to contain an internal explosion. The final items required by the ExTR are controlled documentation of the system and a setup and operating manual. The documentation must be of sufficient detail to show the safety features of the system so that they may be replicated during manufacturing and must match the system that is tested for the ExTR to be valid. The setup and operating manual will ensure that the end user has the necessary written instructions to safely operate the system.
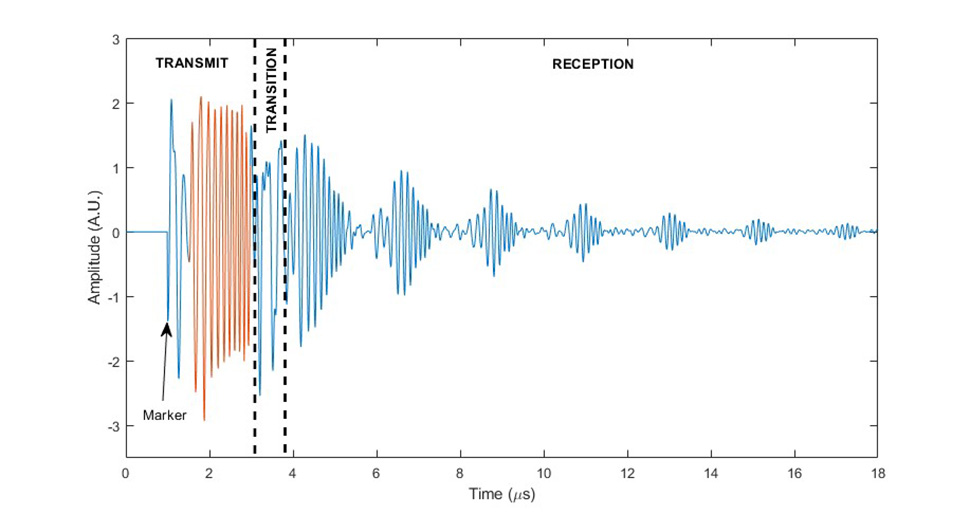
Figure 1: Received signal, including the attenuated transmit signal and multiple reflections received from the backwall.
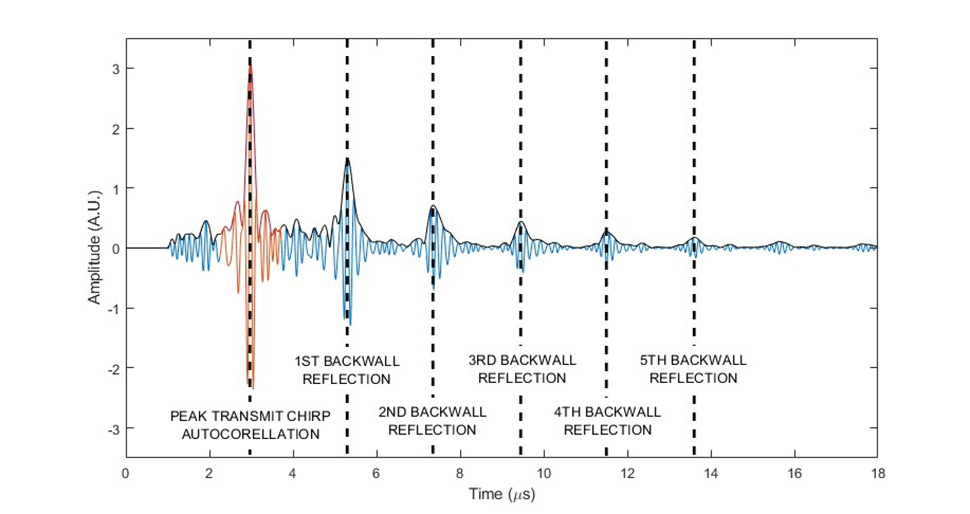
Figure 2: Output of the matched filter showing multiple reflections from the backwall. The solid black line shows the envelope of the filter response; dashed lines at local peaks of the filter output indicate precise times of the backwall signals.
Accomplishments
A prototype system was manufactured. Functional tests on the completed system showed that it met the performance goal of measuring wall thickness for a range of wall thicknesses from 6 mm to 60 mm with a standard deviation of better than 0.1 mm. Physical tests for the IECEx certification on various components of the system have been successfully completed. The IECEx TR documents were completed and the IECEx TR has now been issued.
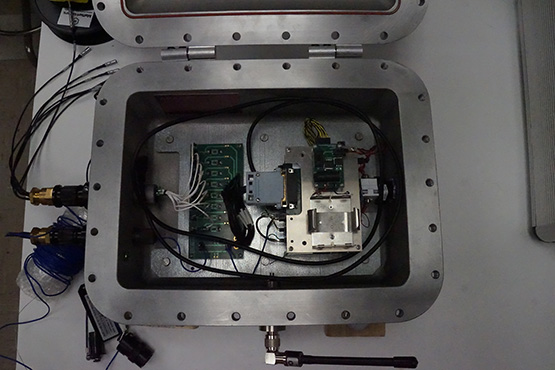
Figure 3: Completed instrument prototype with the lid open. The Wi-Fi antenna is attached to the front exterior of the enclosure; ultrasonic sensor cables and a thermocouple cable are attached to the left side of the enclosure.
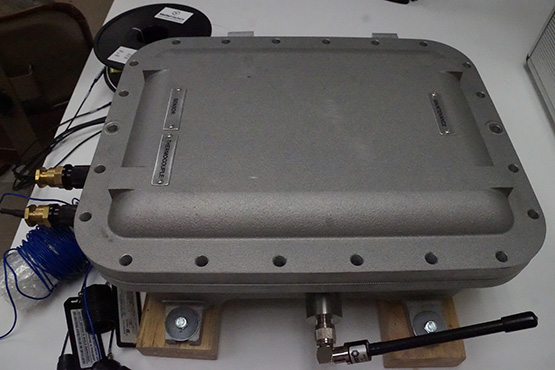
Figure 4: Instrument prototype with the lid closed.